Quality Control software for Manufacturing
A manufacturing quality control software to standardise operator checks for quality that’s right the first time.
Even the best software for quality control in manufacturing can miss in-line defects and trends without operator checks.
Reworks, waste, and human error are the demise of quality metrics, and as any quality team knows, trends are near impossible to spot with retrospective reporting. Spreadsheets are not a reliable manufacturing quality control tool, and many quality control software suites lack an operator-log option.
Reliable manufacturing quality control doesn’t happen by accident. Digital quality checks can minimise human error and prevent defects and reworks downstream. Using LineView’s DigiView quality management solution for manufacturing, quality leaders can schedule checks to record compliance and confirm quality to standard.
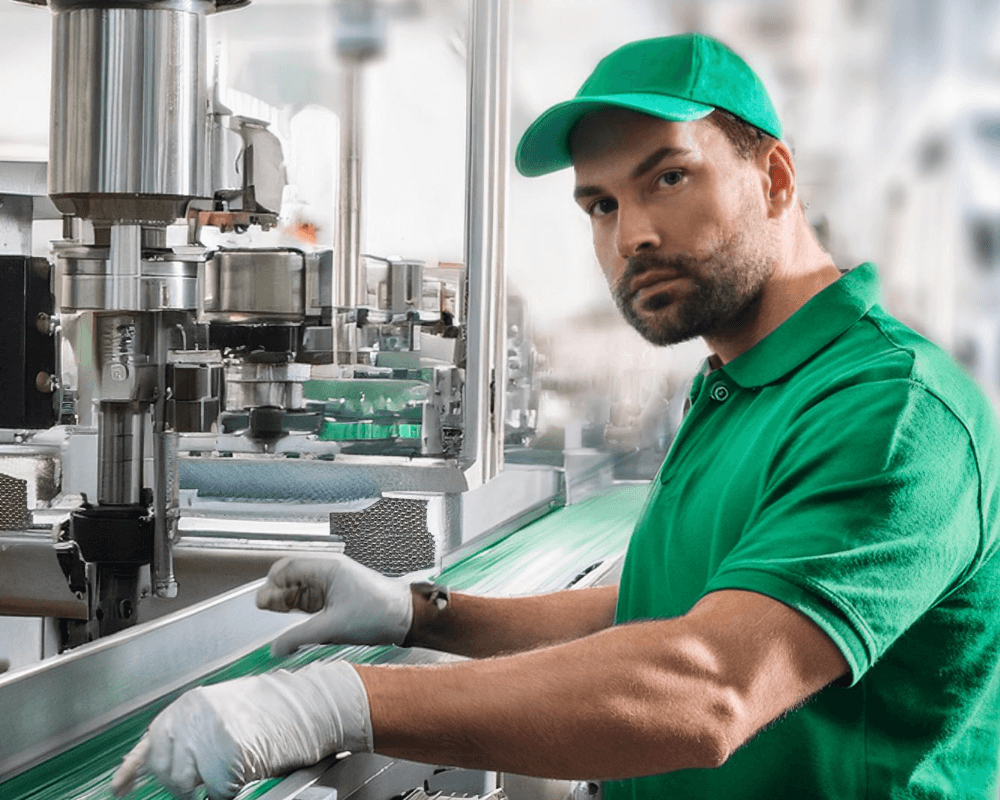
Prevent reworks and waste with quality management software for manufacturing that is 100% audit-ready.
Configurable quality control checks
DigiView uses workstations and roles to match the way you work. User prompts tell operators to complete checks and recheck when required. Manager approval processes confirm data is correct and help guarantee corrective actions.
Line quality checks for compliance and audits
Paper-based quality management in manufacturing is time-consuming with limited traceability, even when you have a LIMS system. Save operator and QC time with templates and processes to simplify ISO and industry compliance.
Quality visualisation and live quality views
What if you could spot a drift in packaging appearance or set-point on an asset? DigiView quality control software for manufacturing offers a live view of performance with historical data that can be correlated with production insights to spot trends and opportunities.
Software for quality control in manufacturing – for today’s shop-floor and your factory of the future.
Manufacturers must adapt to a new way of thinking about manufacturing quality control and quality management systems to stay competitive in today’s global market.
When choosing a manufacturing quality control software today, it should embrace Quality 4.0 practices. These include harnessing end-to-end production data to prepare their factories for long term success and consistent quality.
Standardise parameters for manufacturing quality that’s right the first time.
Paperless manufacturing quality control software empower operators to log inline quality with modern, visual checks. Plus, quality levels improve when leaders can easily access an operator’s shift progress charts with live and historical data.
If you are ready to replace time-consuming paper quality checks and spreadsheet tracking, Lineview’s DigiView manufacturing quality control software is the ideal tool. Schedule checks, record compliance, and confirm quality standards across every production process.
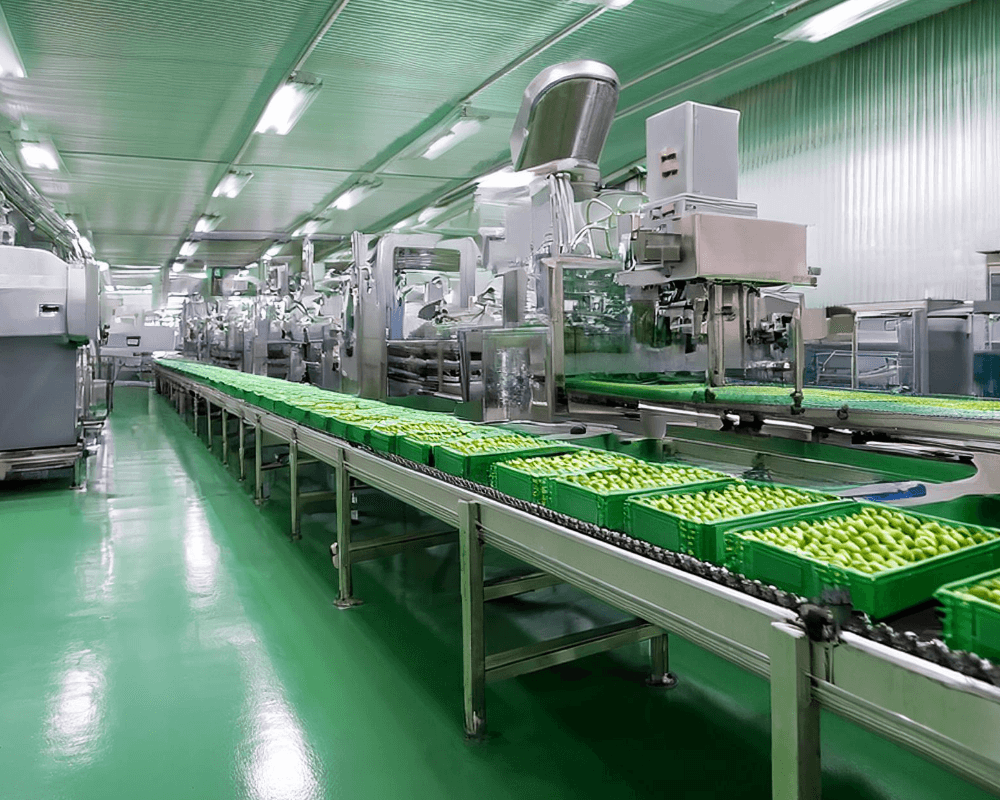
Zero downtime and 10% OEE improvement are easier with causal loss.
Instead of focusing on individual downtime events, Lineview helps you move beyond the symptoms to the true cause of downtime.
Improved OEE, downtime monitoring of microstops, auto fault analysis and productivity tools are the tools your team need for sustainable downtime reduction. And as a bonus? Get a guaranteed 10% efficiency improvement.
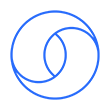
Built-in manufacturing quality control tools for quality standards
Operator prompts and visual checks ensure production within tolerance
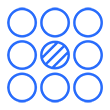
End-to-end audit-ready quality traceability
Trends and quality issues are visualised live and historically
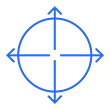
Digital checks to cut human error, defects and reworks
Use video and images as work instructions to guide operators
Customer stories
Dive into how Lineview empowers manufacturers to transform production. We believe success is a two-way street (win-win), so explore how our customers win big, and how their success fuels our drive to keep innovating.
Case Study
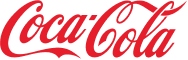
Coca-Cola Enterprises selects Lineview™ as their system of choice.
Over a three-year period, LineView™ has been implemented on every production line in Europe to help increase efficiency and reduce manufacturing costs.
Case Study

AB InBev China achieves Goals through Data, focus and action.
The world’s largest brewer, AB InBev, recommended LineView™ to their Chinese bottling plant based in Wuhan to remedy the company’s struggles with efficiencies.
Case Study
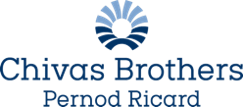
Chivas Brothers Pernod Ricard increases mechanical efficiency by 17% in six months.
Line 33’s Mechanical Efficiency increased from 60% to 70% after six months of data-driven interventions and focused improvements.