Machine Downtime Tracking Software
Get to zero unplanned equipment downtime using causal loss.
Tired of interruptions and limited capacity? Track and prevent machine downtime hampering worker productivity.
When downtime tracking is a mix of manual processes and sensor-based data recording, operational teams can’t easily spot and correct the underlying cause of unplanned equipment downtime. Monitoring production downtime accurately at a granular level requires automated, machine-level data. With better data and proactive interventions, it’s easier to solve the real root cause of equipment downtime – boosting capacity and improving lead times.
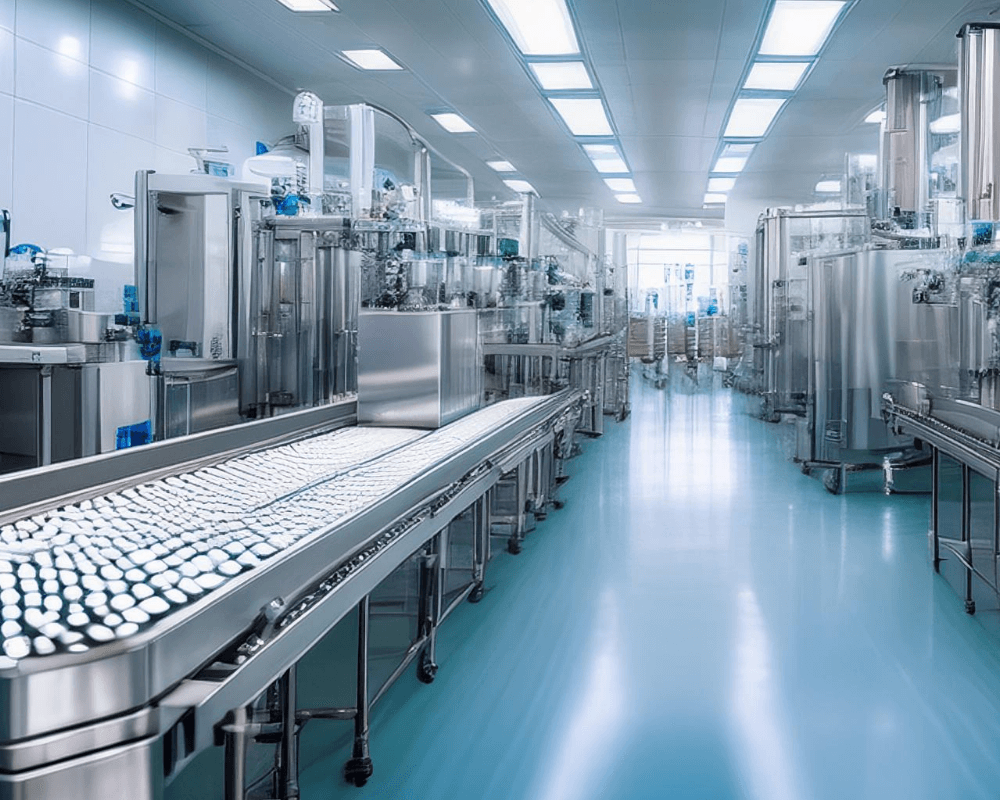
Reduce unplanned downtime without hours of root cause analysis.
Automated PLC data – no bolt-on sensors required
LineView™ machine downtime tracking software is simple to implement, connecting to data you already have without redundant sensors. Once up and running, it enables you to track and reduce downtime rapidly – unlocking additional capacity.
Automatic fault insights without DIY reporting
What’s easier? Hours spent compiling reports or auto fault detection? LineView simplifies OEE as well as downtime tracking and management. Causal loss intelligence and a timeline illustrate exactly when a loss occurs.
Operational excellence built in and on-call
Unlike other machine downtime tracking software, our downtime management solution doesn’t stop at reports. Built-in SIC and equipment downtime tracking routines supported by in-house operational experts will guide your team to lower unplanned downtime.
Tracking downtime is good. Automatically detecting True Causal Loss is better.
Improved equipment downtime tracking is only the first step to better OEE downtime monitoring and management. LineView’s intelligent True Casual Loss algorithm automatically correlates a machine-level fault to the impact on that machine and yourOverall Equipment Efficiency (OEE) score. Further categorising downtime into the six losses of OEE provides an accurate picture of downtime and prioritised actions. By shifting focus from machine downtimes to Causal Loss, continuous improvement teams and operators can move away from reactive interventions that are disruptive and inefficient.
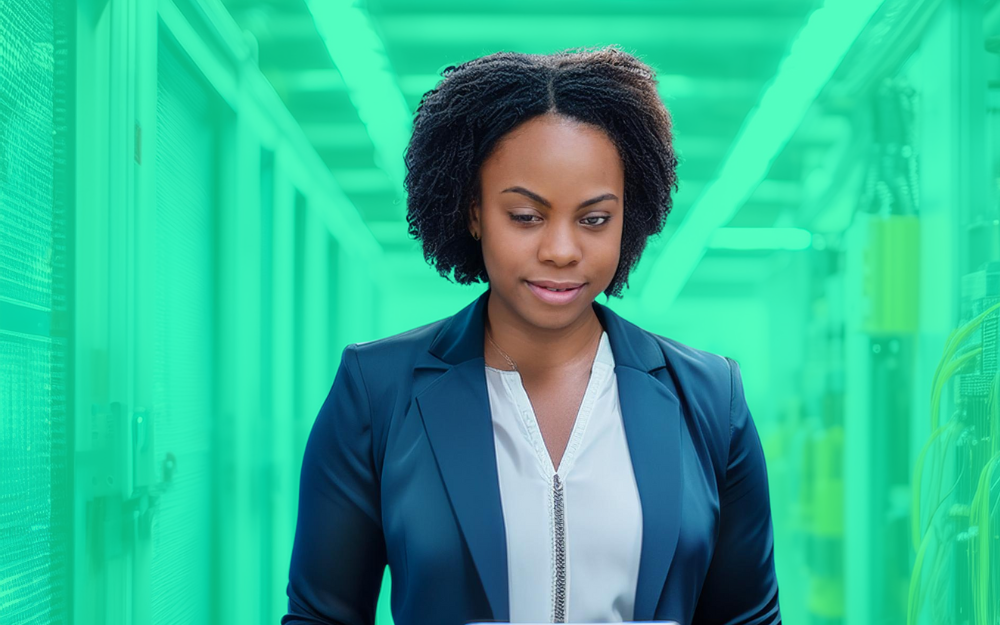
How Downtime Tracking Works:
1. Use LineView’s software to track equipment downtime accurately
Upgrading to automated machine-level downtime tracking and auto-fault detection not only improves production monitoring but also empowers operators and managers with accurate, actionable information – not best guesses.
2. Auto-detect true causes of downtime for more efficient fixes
Armed with the underlying cause of downtime allows teams to fix the constraint on the line instead of the symptoms upstream or downstream.Teams Will save wasted time and labour, benefitting your profitability bottom-line.
3. Optimize management time and worker productivity
Using LineView’s automated casual machine downtime tracking function frees management time to focus on coaching and process improvements. Empowering managers with machine fault-level root causes saves hours of analysis and historical reporting.
4. Speed up changeovers and streamline maintenance planning
Once your team has attacked the largest sources of chronic and intermittent downtime, apply LineView data and tools to changeovers, planned maintenance activities, and other focused improvements.
Zero downtime and 10% OEE improvement are easier with causal loss.
Instead of focusing on individual downtime events, LineView helps you move beyond the symptoms to the true cause of downtime.
Improved OEE, downtime monitoring of microstops, auto fault analysis and productivity tools are the tools your team need for sustainable downtime reduction. And as a bonus? Get a guaranteed 10% efficiency improvement.
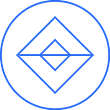
Be proactive to prevent machine downtime
Minimum 10% OEE gains
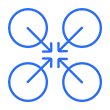
Go beyond symptoms to true causes of downtime
Faster changeovers
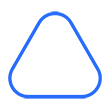
Get accurate unplanned equipment downtime statistics
Reduce (or eliminate) costly microstops
Customer stories
Dive into how Lineview empowers manufacturers to transform production. We believe success is a two-way street (win-win), so explore how our customers win big, and how their success fuels our drive to keep innovating.
Case Study
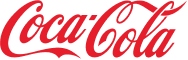
Coca-Cola Enterprises selects Lineview™ as their system of choice.
Over a three-year period, LineView™ has been implemented on every production line in Europe to help increase efficiency and reduce manufacturing costs.
Case Study

AB InBev China achieves Goals through Data, focus and action.
The world’s largest brewer, AB InBev, recommended LineView™ to their Chinese bottling plant based in Wuhan to remedy the company’s struggles with efficiencies.
Case Study
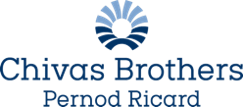
Chivas Brothers Pernod Ricard increases mechanical efficiency by 17% in six months.
Line 33’s Mechanical Efficiency increased from 60% to 70% after six months of data-driven interventions and focused improvements.