Improving OEE in Food Manufacturing.
Consumers are increasingly demanding healthy and inexpensive quality food, traits which don’t naturally align, so food manufacturing efficiency solutions must be sought.
Increased regulations and close governmental monitoring are testing food production facilities’ ability to produce. Changing consumer demand and a growing list of alternative nutrition products are pushing plants to find new efficiencies to maintain flexibility and improve OEE within existing food manufacturing facilities.
- Healthier options and updated packaging have become priorities.
- Manufacturers need to prototype, test and launch new products rapidly to meet consumer trends.
- Recalls are expensive in both the short term but also to long term reputation.
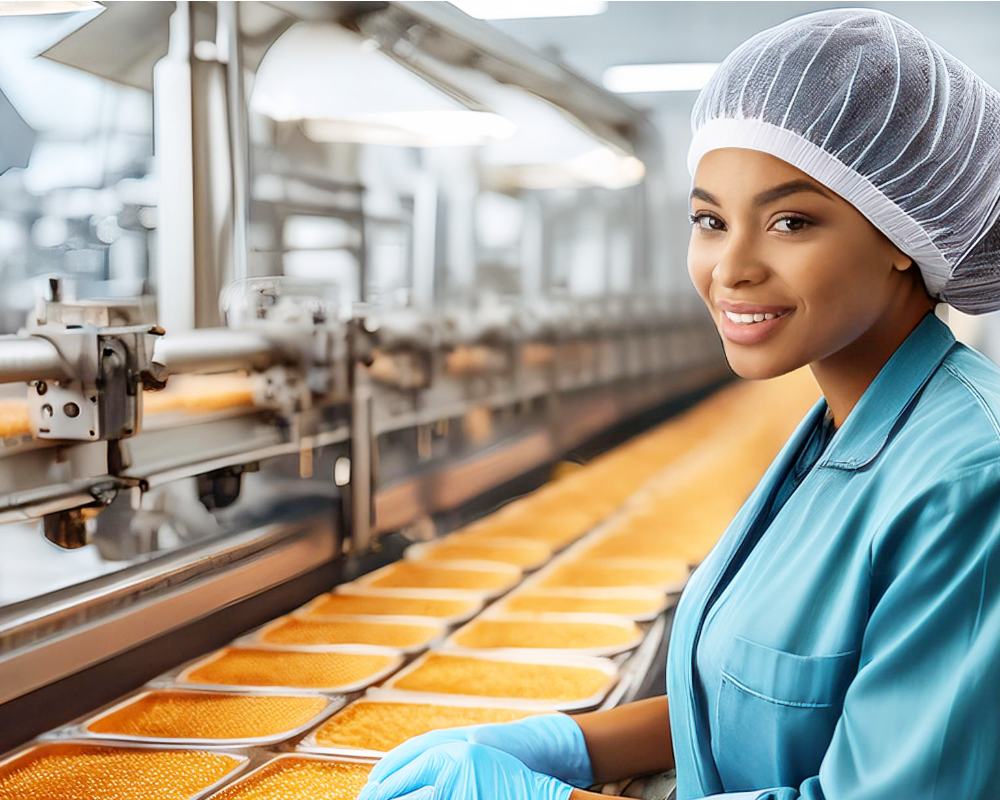
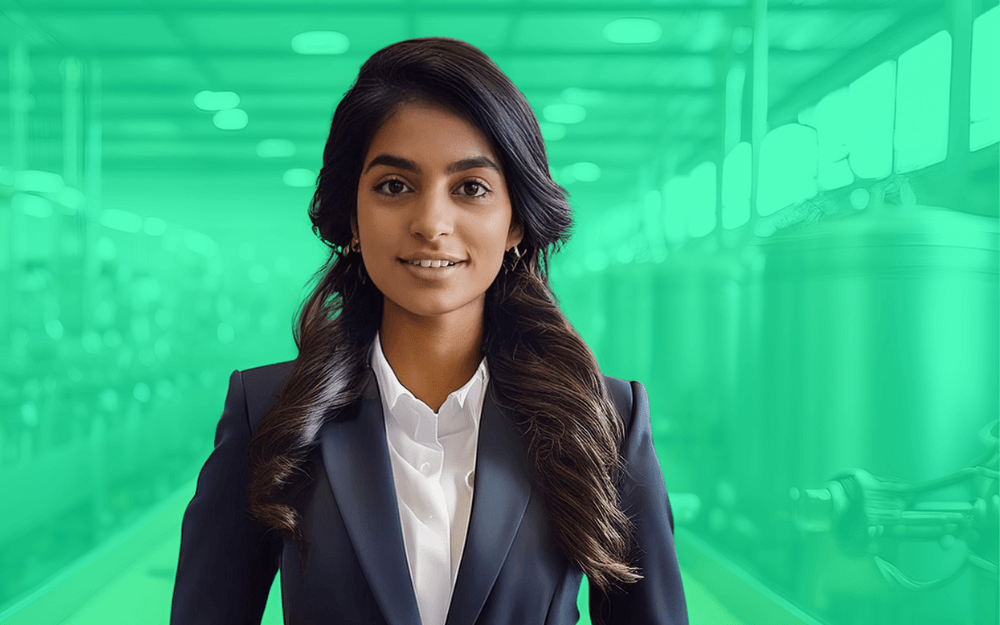
Plant Operations
Plant and Production Management is a balancing act of achieving production improvement gains against daily production challenges and team engagement. With the integration of innovative real-time monitoring food manufacturing efficiency solutions, find significant and rapid KPI improvement gains.
- Significant and rapid KPI improvement gains
- Added insight and innovation on the shop floor
- Boost to area or team’s performance
Senior Management
Optimise your operational structure and routines around the use of data with food manufacturing efficiency software and OEE improvement solutions that deliver actionable information in real-time.
- Support to achieve World Class OEE and Operational Excellence
- Maximised output with existing resources
- Increased visibility across the enterprise
Digital Transformation Leader
Leaders in manufacturing Digital Transformation think beyond a vision and direction for the factory of the future. You’re also developing the backbone of your manufacturing organisation’s digital smart factory architecture to fit into today’s reality on the plant floor. Lineview lets you take control of current digitalisation efforts with a clear path to your smart factory vision.
- Best-in-class smart factory software with practical AI and ML innovations
- Operational support and innovative developments to reach your digitalisation objectives
- Insight from across your global enterprise with industry-wide benchmarking
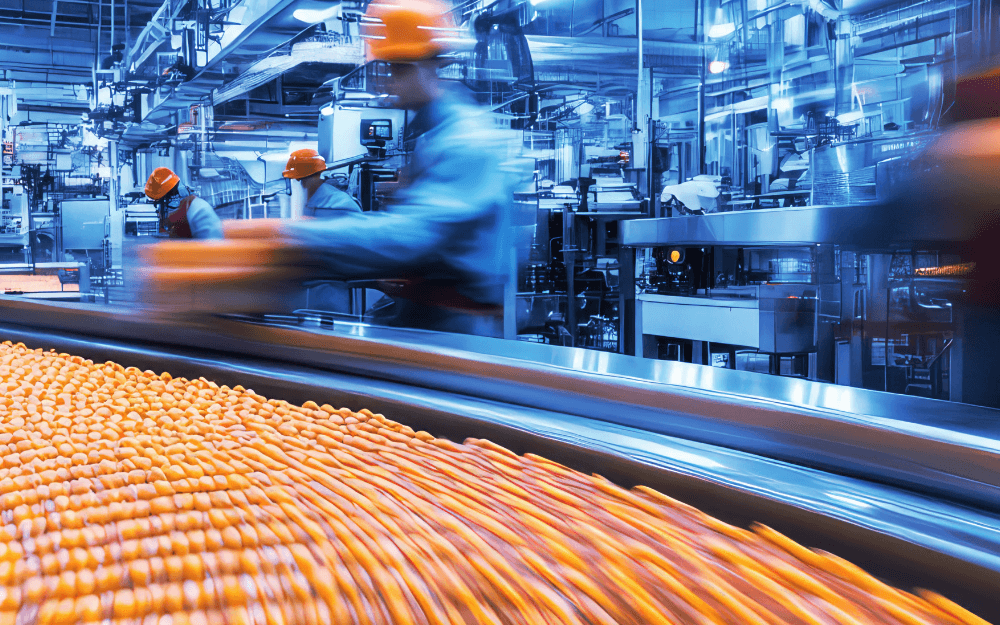
Engineering
Process Engineering in today’s plant is ever-limited by time and capital resources but dictates complex engineering solutions that employ a suite of IT and OT tools. Gain valuable insight with an OEE software for food manufacturers, which provides you with a detailed understanding of individual asset performance and correlation to overall output.
- Measurement and improvement of maintenance and engineering KPI
- Identification of what is a maintenance versus an operational issue and prioritise resources
- Insight without a drain on internal engineering resources
Continuous Improvement
Continuous Improvement success is derived from cost savings and project ROI but you need buy-in from operators and supervisors. Validate your SMED, Kaizen, downtime reduction and machine efficiency CI projects with food manufacturing software and management solutions to quantify your success.
- System to identify and quantify Continuous Improvement initiatives
- Measurement and validation of Continuous Improvement activities
- Ongoing adherence and process optimisation
Customer stories
Dive into how Lineview empowers manufacturers to transform production. We believe success is a two-way street (win-win), so explore how our customers win big, and how their success fuels our drive to keep innovating.
Case Study
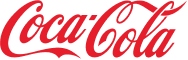
Coca-Cola Enterprises selects Lineviewâ„¢ as their system of choice.
Over a three-year period, LineViewâ„¢ has been implemented on every production line in Europe to help increase efficiency and reduce manufacturing costs.
Case Study

AB InBev China achieves Goals through Data, focus and action.
The world’s largest brewer, AB InBev, recommended LineView™ to their Chinese bottling plant based in Wuhan to remedy the company’s struggles with efficiencies.
Case Study
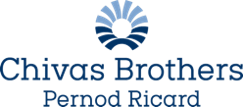
Chivas Brothers Pernod Ricard increases mechanical efficiency by 17% in six months.
Line 33’s Mechanical Efficiency increased from 60% to 70% after six months of data-driven interventions and focused improvements.