OEE Improvement
Categorise OEE losses into various metrics to easily target areas of improvement
Wouldn’t it be amazing if all equipment would operate all the time at full capacity producing good quality product?
Overall Equipment Effectiveness is a measure of what you actually made over what you could have made, in theory, over that timeframe. The difference between the ideal (theoretical) and actual situation is due to losses categorised into various metrics that provide you with excellent data to enable you to target areas of the OEE improvement plan.
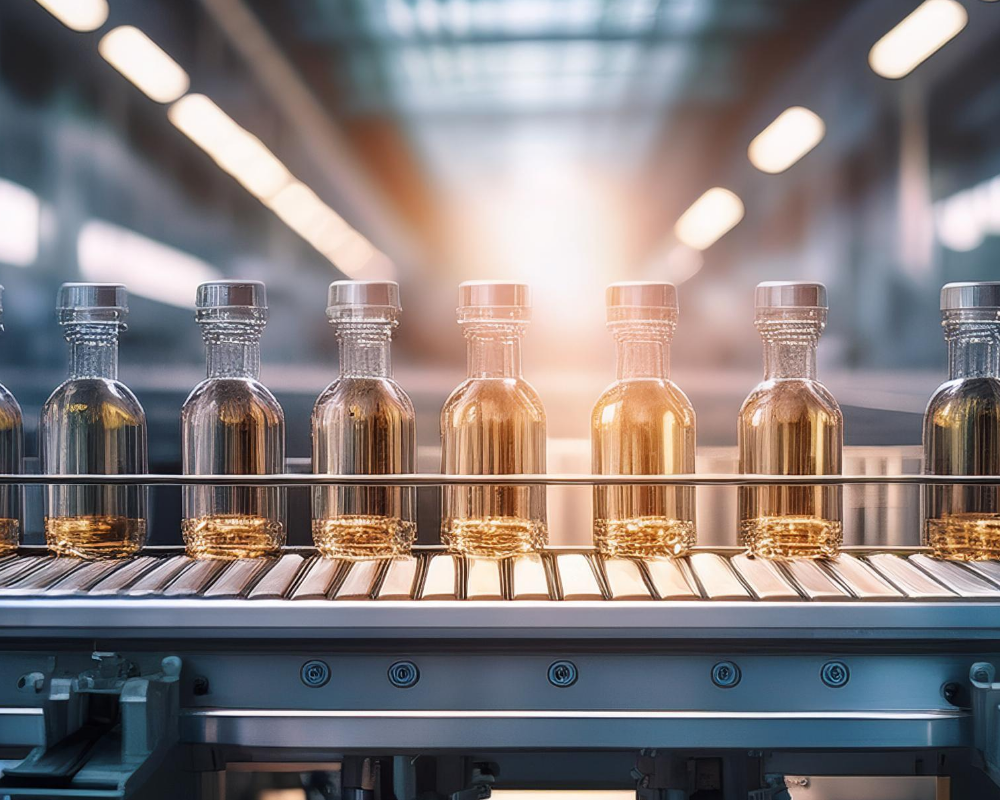
Reduce or eliminate the six losses of OEE and improve your score with OEE improvement strategy.
Understanding and categorising efficiency loss into six losses pinpoints area of focus that will improve the efficiency of the equipment. These six losses contribute to your OEE score and are categorized under Availability, Performance and Quality Loss.
What are the six losses of OEE?
- Planned downtime or external unplanned event
- Speed loss
- Breakdowns (>5mins)
- Minor stops (<5mins)
- Production rejects
- Rejects on start up
Calculate your Overall Equipment Effectiveness (OEE)
OEE is a widely used measure to determine performance against equipment capability. Factoring the metrics Availability, Performance and Quality, the better OEE improvements – the closer your efficiency is to World-Class performance.
Availability is a measure of the time the equipment was actually available to run within the specified duration, generally known as planned production time. The time it is not available is generally attributed to large duration of downtime such as product changeovers, breaks, breakdowns, etc.
Performance is a measure of how well the equipment performed when it was running. The loss of time in this category is mainly due to the equipment not running at its required rate and so producing products at a reduced rate.
Quality is a measure of time taken to produce a good quality product. The loss in this category is due to time lost to make inferior quality product.
OEE = A x P x Q
Optional Calculations
Operating Time
Planned Production Time
AVAILABILITY is a measure of the time equipment was actually available to run within the specified duration generally known as planned production time.
Net Operating Time
Operating Time
PERFORMANCE is a measure of how well the equipment performed when it was running.
Fully Productive Time
Net Operating Time
QUALITY is a measure of time taken to produce good quality product.
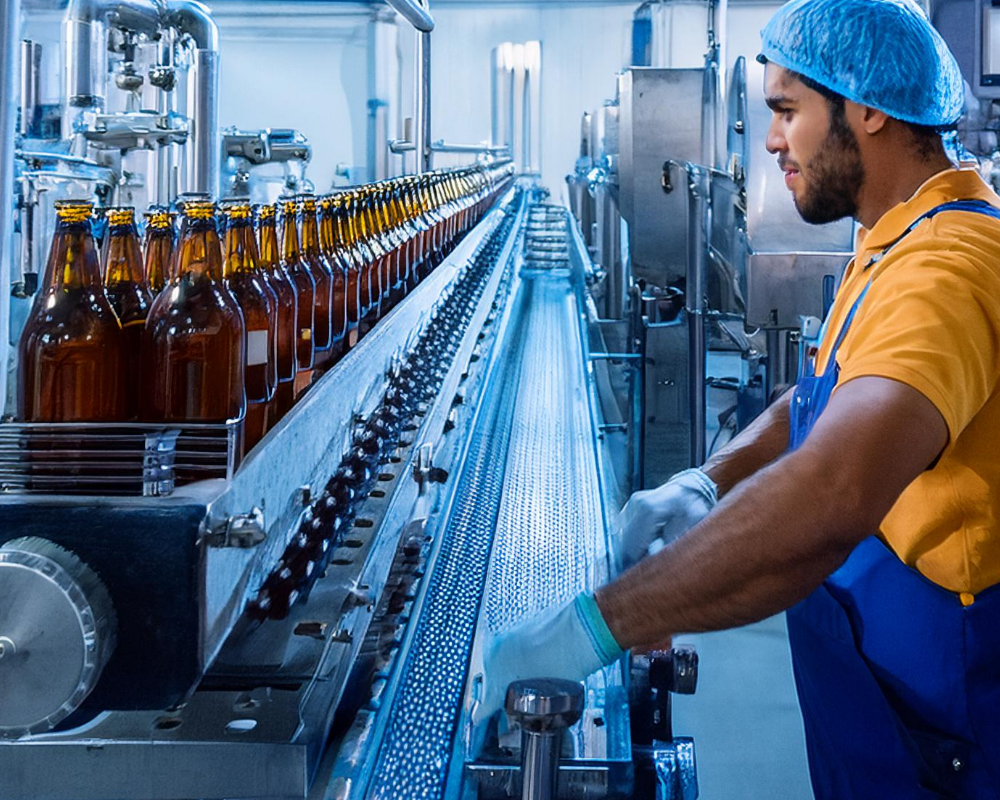
Sustainability challenges and resource optimization
Sustainability goes beyond greenwashing; global governmental bodies are enforcing stricter environmental laws and reporting.
Moreover, the availability of raw materials such as ground water is reducing each day. 1 out of 3 manufacturing plants are in water scarce regions. LineVvew understands your commitment towards net zero carbon emissions and reducing water & energy wastage. By optimizing plant processes, Lineview minimizes resource use and emissions while enhancing productivity.
Digital transformation made easy
We recognize that not everyone is tech-savvy. That’s why LineView is user-friendly and intuitive. Our expert team collaborates with you, allowing you to focus on your work while improving results. Unlike traditional MES or SCADA systems, LineView offers fast and easy ROI. Out-of-the-box insights empower team leaders to focus on actions rather than time-consuming DIY reporting. Plus, teams can immediately see the impact of their actions, leading to faster order-to-delivery times.
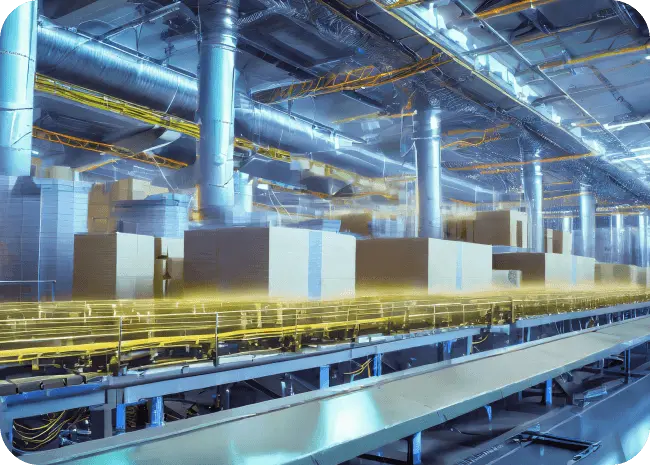
Customer stories
Dive into how Lineview empowers manufacturers to transform production. We believe success is a two-way street (win-win), so explore how our customers win big, and how their success fuels our drive to keep innovating.
Case Study
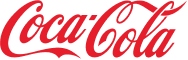
Coca-Cola Enterprises selects Lineviewâ„¢ as their system of choice.
Over a three-year period, LineViewâ„¢ has been implemented on every production line in Europe to help increase efficiency and reduce manufacturing costs.
Case Study

AB InBev China achieves Goals through Data, focus and action.
The world’s largest brewer, AB InBev, recommended LineView™ to their Chinese bottling plant based in Wuhan to remedy the company’s struggles with efficiencies.
Case Study
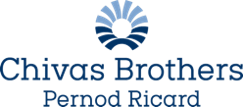
Chivas Brothers Pernod Ricard increases mechanical efficiency by 17% in six months.
Line 33’s Mechanical Efficiency increased from 60% to 70% after six months of data-driven interventions and focused improvements.