Production OEE Software
Drive production efficiency with better data collection, OEE software for manufacturing and a team of helpful experts
It’s hard to find time to monitor equipment performance when you’re putting out fires and fixing bottlenecks.
It’s difficult to meet daily production demands when teams are up against supply chain disruptions and labour shortages. Finding time to compile data, input manual tracking, and run reports is impossible. LineView’s OEE monitoring software goes beyond downtime tracking, six loss, and root cause analyses to deliver actionable insight-for instance, the true cause of your OEE production efficiency losses and where to focus your continuous improvement efforts. Our efficiency experts will help you achieve rapid improvement wins and world-class OEE with reliable data and a best-of-breed Overall Equipment Effectiveness tracking and reporting software.
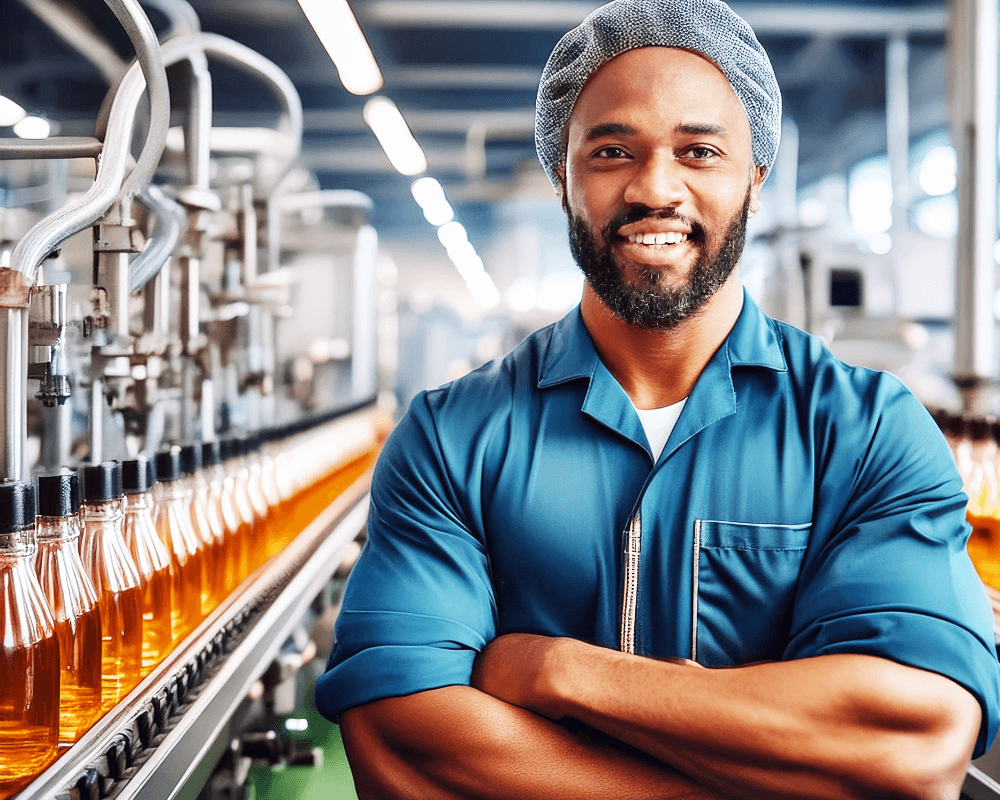
Empower your leaders and operators to make systematic OEE improvements.
Targeted, actionable OEE insights and KPI
Ready to move beyond manual or historical KPI to advanced OEE software with causal loss? LineView is a full-function production OEE monitoring system for high-speed filling lines. With solid data and actions we expect a 10% OEE boost.
Operational support to guide OEE improvement
Real-time OEE insight from OEE reporting software helps operators spot problems before they become persistent. Bringing awareness about OEE to everyone in your organization takes shared OEE goals and standards. We Will help your team thrive with training and management routines.
Automated data collection with integrated operator tools
LineView’s OEE data collection software for manufacturing leverages the PLC data you already have without costly sensors. With automated data -including live line status and drill down to first-fault causal loss – you’ll get the most accurate OEE. Learn Why LineView is the industry’s OEE monitoring solution.
Eliminate production loss with a solid OEE improvement strategy and OEE monitoring software.
From micro-stops causing downtime to misalignments reducing speed, mistaking symptoms as the root cause of poor Overall Equipment Effectiveness scores is common.
LineView’s OEE data collection software and monitoring solutions provide the data, visibility, and insight to focus on the right six loss improvements. With a proper strategy, operational support, and our leading OEE software, we can expect a 10% boost in your OEE score.
How OEE software works:
1. Automate OEE data collection to track and record causes of loss
Connect directly to the machines’ PLC data you already have, to save cost of additional sensors and ensure you’re working with the most accurate, actionable dataset. With a visual factory and all your core KPIs in one place, you’re always in control with OEE manufacturing software: Output, Efficiency, and Loss at your fingertips.
2. Use OEE software loss analysis drilldown to find the hidden causes of OEE loss
A move to automated casual downtime function and first-fault detection improves production OEE monitoring. Real-time six loss analysis splits your losses into categories to enable targeted improvement activities and effective decisions. Armed with the underlying cause of downtime and other production losses, your team can fix the underlying constraint rather than the symptoms – saving time and labor wasted on needless fixes and minor inefficiencies.
3. Improve OEE visibility and reporting to drive engagement
Built-in OEE reports, a tactical reports builder and enterprise-wide reporting, mean you and your operators can easily leverage the simplicity of OEE alongside the power of our LineView-generated insights. Machine diagnostics and a built-in machine status dashboard of our OEE software are powerful tools to summarize individual machine performance and machine KPI on a single screen. Use the status screen to easily identify individual downtime and how it has affected total output.
4. Get training and a performance boost from our OEE experts
Having the right data at the right time in the right place using LineView’s OEE software is a great first step towards manufacturing efficiency improvement. Working With operational excellence experts takes thosewins to the next level. LineView’s team will help you put the right routines into place, increase engagement and manage performance on the shop floor. It’s a winning combination for great production, every day.
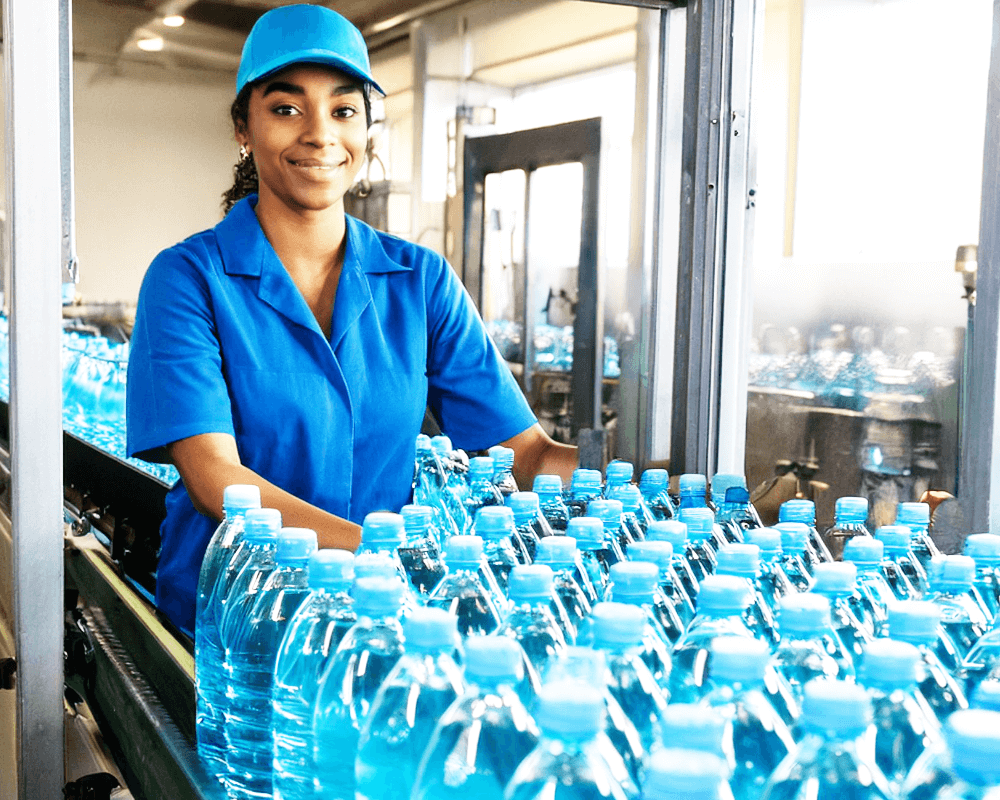
Upgrade to an advanced OEE software-fully supported by our helpful team of OEE experts.
Data isn’t practical if your team can’t see it until the next production meeting or if it’s missing critical areas of OEE loss. Real-time OEE with visual cues is helpful to you and your operators – but advanced OEE software with live line status, drill down to causal loss, and connected operator tools is a powerful tool for your lines.
We expect to see a minimum step change in OEE of 10% with LineView OEE manufacturing software. Why do we stand behind this? Because We have proven results across hundreds of line installations to increase capacity and reduce cost.
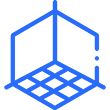
See a live shop-floor view with a drill down to issues
10% OEE improvement expected
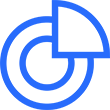
Optimise your operations team’s full potential
Unlock production capacity with LineView’s OEE software solutions
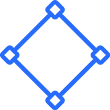
Connect to PLC data-no missing data or manual tracking
Real-time OEE data monitoring, collection and reporting
Customer stories
Dive into how Lineview empowers manufacturers to transform production. We believe success is a two-way street (win-win), so explore how our customers win big, and how their success fuels our drive to keep innovating.
Case Study
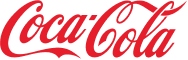
Coca-Cola Enterprises selects Lineviewâ„¢ as their system of choice.
Over a three-year period, LineViewâ„¢ has been implemented on every production line in Europe to help increase efficiency and reduce manufacturing costs.
Case Study

AB InBev China achieves Goals through Data, focus and action.
The world’s largest brewer, AB InBev, recommended LineView™ to their Chinese bottling plant based in Wuhan to remedy the company’s struggles with efficiencies.
Case Study
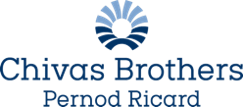
Chivas Brothers Pernod Ricard increases mechanical efficiency by 17% in six months.
Line 33’s Mechanical Efficiency increased from 60% to 70% after six months of data-driven interventions and focused improvements.