Smart Manufacturing for your Enterprise
LineView™: Our flagship one-stop solution for digital transformation in manufacturing.
Unlock the true potential of your manufacturing plants with LineView, our transformative platform. LineView has been the trusted solutions partner of most advanced manufacturers for over 2 decades.
LineView streamlines even the most intricate, high-speed production processes. It empowers sustainable practices and data-driven decisions, all in one unified platform, to unlock peak performance.
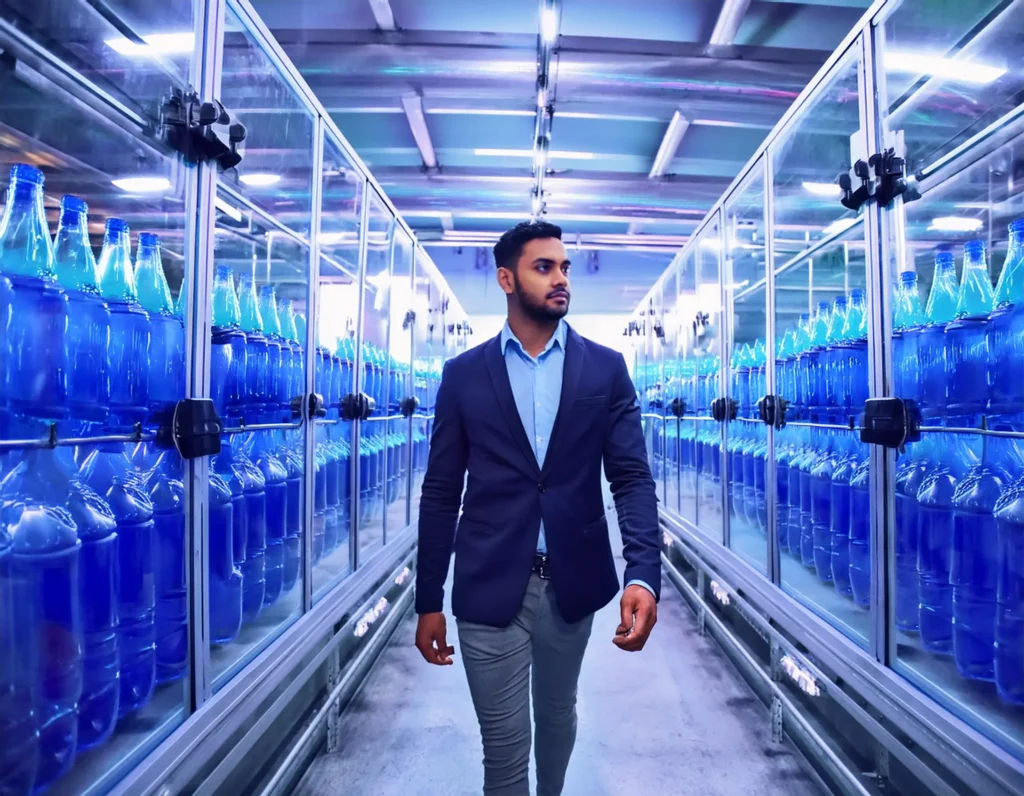
LineView: One platform, many solutions
LineView is the only manufacturing efficiency software that identifies the highest impact opportunities for productivity gains on bottling and packaging lines. LineView is designed to adapt to the most complex and high-speed production lines, optimize your cost of production and strengthen your sustainability initiatives.
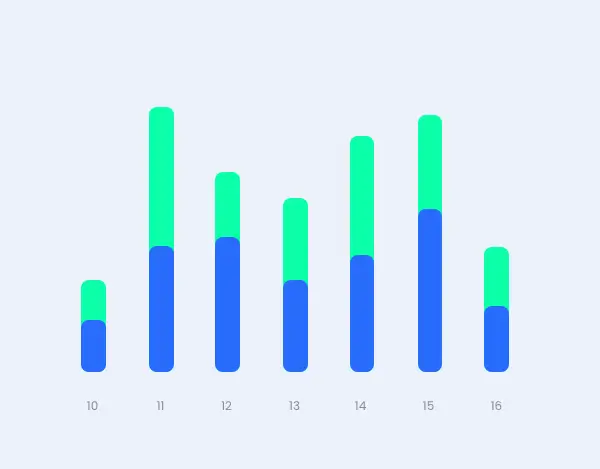
AUTOMATED INSIGHTS
The focus your team needs to make good decisions on the fly.
LineView simplifies decision-making and strategy for everyone on the production team. Its automated insights are tailored to each role, from line workers to plant managers, giving everyone the information they need to succeed.
Shift and team leaders often lack the time for extensive KPI analysis and reporting. LineView automated insights allow them to focus on targeted improvement actions. LineView provides True Causal Loss analysis and the ability to identify emergent opportunities in production lines.
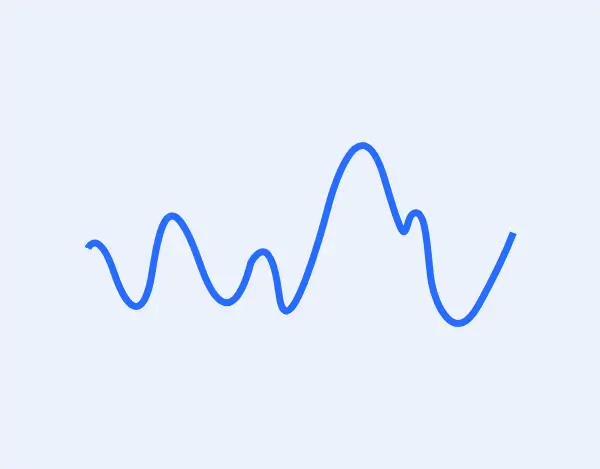
DATA & PERFORMANCE TOOLS
It’s your data. Use it to unlock capacity & savings.
We believe manufacturing efficiency systems should include everything needed to maximize productivity. LineView provides both data and performance tools to unlock capacity and savings. With live line status, drill downs to first-fault causal loss and built-in routines for instant decisions, there’s a good reason LineView is the leading software for performance improvement and OEE gains on bottling and packaging lines.
Read more
Data is often referred to as the new oil, and Lineview equips your CIO and Data officers with an extensive dataset for analysis. Moreover, it provides insights into the subtle production and supply chain issues that might otherwise remain unnoticed.
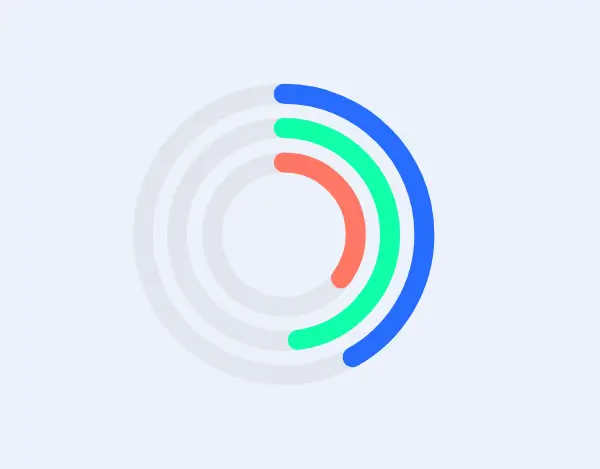
OPERATIONAL EXCELLENCE BUILT-IN
Not just OEE software. A game-changing approach to productivity and sustainability.
Our team understands the challenges of bottling and packaging efficiency because we’ve been there. Built by operations experts as a holistic approach to improving production performance, LineView puts operational excellence best practices at the foundation of each roll-out. Twenty years later, we have proven results across the world’s largest packaging brands.
Read more
LineView extends beyond mere productivity improvement software; it generates a significant impact beyond the production hall. We refer to this as the Ripple effect. LineView serves as the central hub of your manufacturing ecosystem, seamlessly connecting with your ERP system and poised for action. Moreover, LineView provides the groundwork for sustainability initiatives, whether that involves reducing water usage, minimizing carbon footprint, or optimizing energy consumption.
See LineView in action
Digital Transformation is inevitable in manufacturing and LineView makes it seem simple.
Unified Solutions: LineView’s Compact Multifunctionality
LineView provides applications to unlock manufacturing efficiency improvements across your operations, improve sustainability metrices and drive strategy at organisation level.
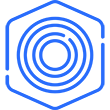
Data-Driven Management Routines
Retrospective data analysis is time-consuming for you and your managers. Meetings and routines linked to real-time data eliminate wasted time – resulting in more efficient, productive meetings.
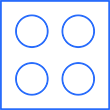
Machine Downtime Tracking Software
LineView™ machine downtime tracking software is easy to implement, leveraging existing data without redundant sensors. Once operational, it enables rapid downtime reduction, unlocking additional capacity.
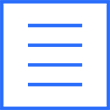
Production Line Balance Optimization & V-Curve
Our team doesn’t stop at mere production line balancing software. We guarantee a step-change in the manufacturing line balance. Through a data-informed audit, five levels of control implementation, and team training, LineView’s line balancing software delivers long-term results.
Production Line Monitoring Software
Boost line and equipment efficiency with our advanced OEE system, which pinpoints Causal Loss down to the first fault. Make data-driven decisions without extensive analysis.
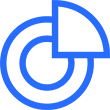
Visual Factory Software
The line overview overlays your core KPI onto a graphic of your line that doubles as a screen display. Color-coded cues indicate trends, with a drill down to root cause including high-resolution automated trending of PLC fault codes.
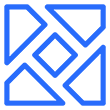
SIC built on industry-proven approach
Short Interval Control (SIC) extends the function of daily production meetings. The proven approach accelerates improvements, empowering operators with structured data and responsibility.
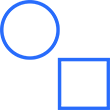
Operational excellence built in and on-call
Unlike other machine downtime tracking software, our downtime management solution doesn’t stop at reports. Built-in SIC and equipment downtime tracking routines supported by in-house operational experts will guide your team to lower unplanned downtime.
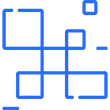
Automatic fault insights without DIY reporting
What’s easier? Hours spent compiling reports or auto fault detection? LineView simplifies OEE as well as downtime tracking and management. Causal loss intelligence and a timeline illustrate exactly when a loss occurs.
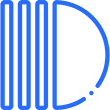
Optional controls to automate restarts and recover speed
Optional manufacturing line balance control unlocks additional performance gains between 2-5%. This supervisory line control module sets optimal restart times on core machines (filler, labeler, packer) to accelerate recovery after downtime.
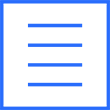
Line balance scores make benchmarking easy
LineView’s software simplifies production line balancing, providing clear balance scores for each product type. It includes baseline comparisons and allows teams to benchmark live data against historical records, ensuring lasting efficiency gains.
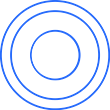
Clean-in-Place and energy insights
Clean-in-place monitoring and energy monitoring are the ultimate add-ons for high-speed filling lines. Lowering energy ratios, reducing effluent, and saving cleaning materials is a win-win for sustainability targets and your bottom line.
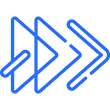
Operator tools and leader routines to drive change
Dashboards are great, but siloed data doesn’t impact change. LineView pairs accurate KPI with operator comments, action logs, and built-in short interval control. With the help of our coaches, your team will be motivated and equipped for productivity improvement.
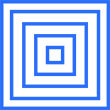
Add-ons for a completely integrated visual factory system
Your visual factory management can be a single source of truth for everything. Not just line monitoring, on-screen displays, and alerts, LineView can serve up reports, energy ratios, clean-in-place trends, and even slow-motion video replays of machine faults.
Customer stories
Dive into how LineView empowers manufacturers to transform production. We believe success is a two-way street (win-win), so explore how our customers win big, and how their success fuels our drive to keep innovating.
Case Study
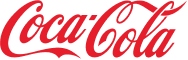
Coca-Cola Enterprises selects Lineview™ as their system of choice.
Over a three-year period, LineView™ has been implemented on every production line in Europe to help increase efficiency and reduce manufacturing costs.
Case Study

AB InBev China achieves Goals through Data, focus and action.
The world’s largest brewer, AB InBev, recommended LineView™ to their Chinese bottling plant based in Wuhan to remedy the company’s struggles with efficiencies.
Case Study
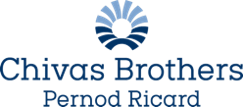
Chivas Brothers Pernod Ricard increases mechanical efficiency by 17% in six months.
Line 33’s Mechanical Efficiency increased from 60% to 70% after six months of data-driven interventions and focused improvements.