Production line monitoring software.
Top-rated real-time production line monitoring system for filling and packaging line performance.
Don’t be limited by your current production capacity and constraints.
Without constant production line monitoring and visibility across the value chain, it’s impossible to understand everything happening on your filling line. Blind spots in data create chaos on the line – Continuous Improvement teams don’t know where to focus, and poor decisions can make a dip in performance even worse.
Consistent operating procedures and real-time line insight motivates teams to win the shift and get the most out of your high-speed filling line.
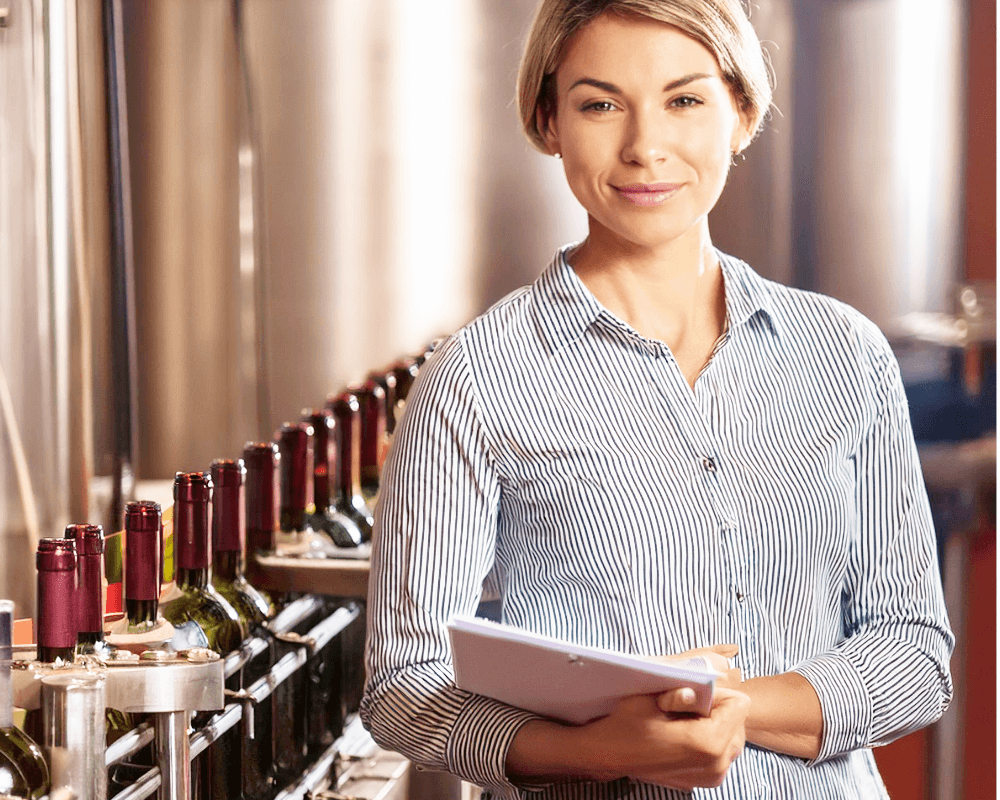
Use the only all-in-one production line monitoring system for high-speed filling lines.
OEE and True Causal Loss for easy efficiency gains
Need more efficient line and equipment utilisation? Our advanced OEE with Causal Loss down to the first fault is a robust production monitoring system for high-speed filling lines. Let your data guide better decisions without hours and hours of analysis.
Clean-in-Place and energy insights to cut energy waste
Clean-in-place monitoring and energy monitoring are the ultimate add-ons for high-speed filling lines. Lowering energy ratios,reducing effluent, and saving cleaning materials is a win-win for sustainability targets and your bottom line.
Line balance optimisation and control for instant capacity
Setting and maintaining optimal line balance control unlocks an additional 2-5% performance gain. Get insight and optional automation to set optimal restart times on core machines and accelerate recovery after downtime.
Built by operation leaders to improve high-speed filling line performance – with teams to guide you there.
When sourcing a production line monitoring solution, available choices are either a lightweight downtime monitoring software or an entire MES/SCADA system. Either way, it’s up to you and your team to build out reports and dashboards, spending valuable management time spotting trends in the chaos.
LineView shows you where to look. The system generates insight and opportunities without time-consuming data analysis. Have a specific improvement project, challenge, or goal? Our team of hands-on experts is ready to guide your team to best-in-class filling line performance.
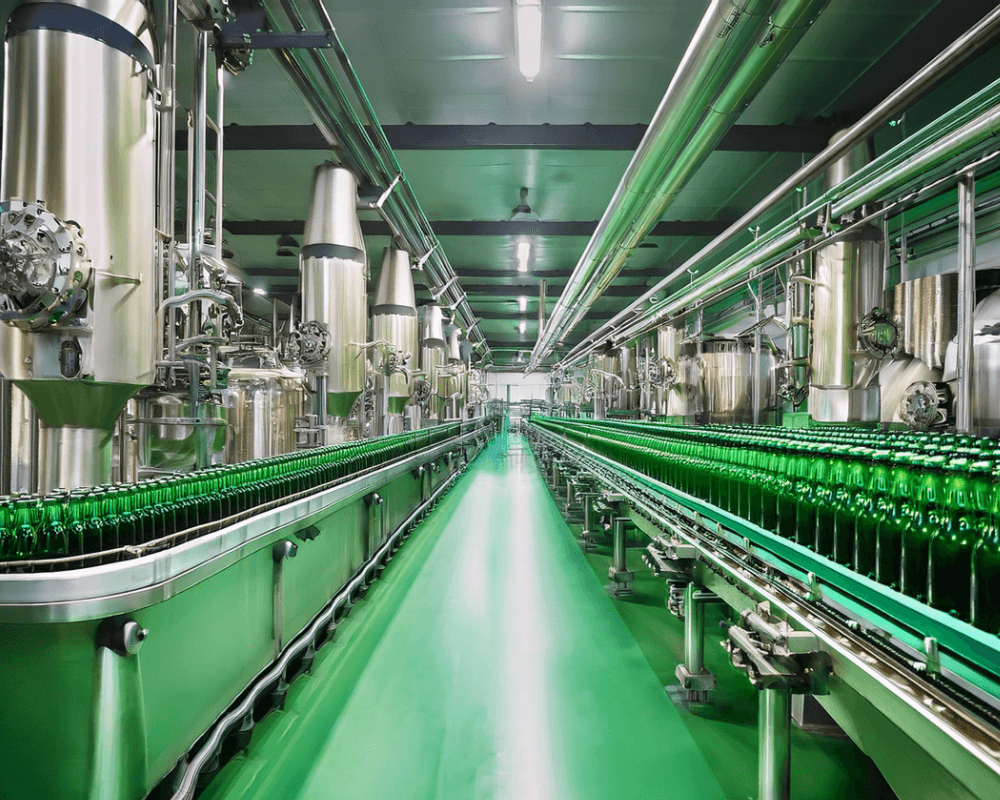
How production line monitoring works:
1. Establish your baseline and connect production line monitoring software directly to PLC data
Unlike data loggers and add-on sensors, LineView production line monitoring solution connects automatically to your PLCs. We’ll conduct an initial site audit to optimise your connection, identify instant wins and prioritise which efficiency opportunities to tackle first.
2. Get the most from your production monitoring system – and your people
Training your team is more than teaching operators to use the system. Our implementation and training are designed to build more effective teams. We’ll teach your leaders to make decisions based on data and introduce them to the management routines we’ve proven at global bottling and packaging sites.
3. Empower your front-line and management teams to win the shift
Our unique combination of specialty manufacturing monitoring software and proven management routines is the secret path to lower costs on your filling line. Hold better production meetings and have interval-based interventions. Your entire team will focus on improving performance – helping you to get the same gains as the world’s leading bottling companies in no time.
4. Take efficiency wins to the next level across your filling line
We guarantee 6-10% ROI in the first six months, but those jaw-dropping results don’t end after the initial installation. Keep the momentum going with the full support of our team for production line monitoring and management software. Plus, modular add-ons mean you can start small and make incremental continuous improvement when you’re ready.
Your 10% OEE gain is just the beginning of your line performance winning streak.
We’ve cracked the code to better bottling line monitoring and performance. Sustainable downtime reduction and efficiency improvements are paired with easy ROI on ancillary processes and CI projects.
Higher-performing teams and more productive high-speed filling lines are just one click away.
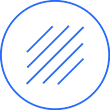
24/7/365 production line monitoring and insights
Identify losses and cost savings
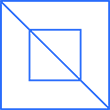
Max throughput with lower operating costs
Gain bottling capacity without CapEx
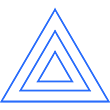
Make your filling line efficiency best in class
Optimise CIP, energy ratios and line balance
Customer stories
Dive into how Lineview empowers manufacturers to transform production. We believe success is a two-way street (win-win), so explore how our customers win big, and how their success fuels our drive to keep innovating.
Case Study
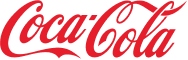
Coca-Cola Enterprises selects Lineview™ as their system of choice.
Over a three-year period, LineView™ has been implemented on every production line in Europe to help increase efficiency and reduce manufacturing costs.
Case Study

AB InBev China achieves Goals through Data, focus and action.
The world’s largest brewer, AB InBev, recommended LineView™ to their Chinese bottling plant based in Wuhan to remedy the company’s struggles with efficiencies.
Case Study
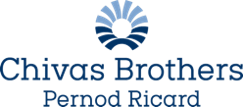
Chivas Brothers Pernod Ricard increases mechanical efficiency by 17% in six months.
Line 33’s Mechanical Efficiency increased from 60% to 70% after six months of data-driven interventions and focused improvements.