Software de seguimiento del tiempo de inactividad de la máquina
Llega a cero paradas no planificadas de los equipos utilizando la pérdida causal.
¿Cansado de interrupciones y capacidad limitada? Controla y evita los tiempos de inactividad de las máquinas que obstaculizan la productividad de los trabajadores.
Cuando el seguimiento del tiempo de inactividad es una mezcla de procesos manuales y registro de datos basado en sensores, los equipos operativos no pueden detectar y corregir fácilmente la causa subyacente del tiempo de inactividad no planificado de los equipos. Supervisar con precisión el tiempo de inactividad de la producción a un nivel granular requiere datos automatizados a nivel de máquina. Con mejores datos e intervenciones proactivas, es más fácil resolver la verdadera causa raíz del tiempo de inactividad de los equipos: aumentar la capacidad y mejorar los plazos de entrega.
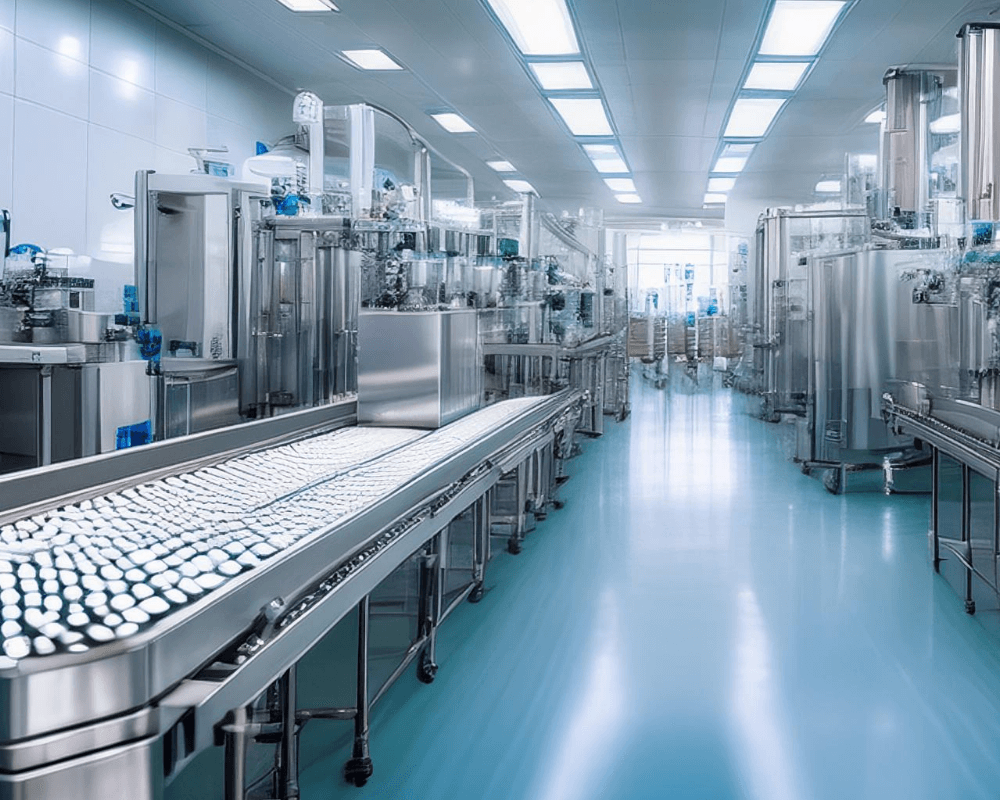
Reduce el tiempo de inactividad imprevisto sin horas de análisis de la causa raíz.
Datos automatizados del PLC: no se necesitan sensores atornillados
El software de seguimiento de los tiempos de inactividad de las máquinas LineView™ es fácil de implantar, ya que se conecta a los datos que ya tienes sin necesidad de sensores redundantes. Una vez en funcionamiento, te permite seguir y reducir rápidamente los tiempos de inactividad, desbloqueando capacidad adicional.
Detección automática de fallos sin informes de bricolaje
¿Qué es más fácil? ¿Las horas dedicadas a compilar informes o la detección automática de averías? LineView simplifica la OEE, así como el seguimiento y la gestión de los tiempos de inactividad. La inteligencia causal de pérdidas y una línea de tiempo ilustran exactamente cuándo se produce una pérdida.
Excelencia operativa integrada y de guardia
A diferencia de otros programas de seguimiento de paradas de máquinas, nuestra solución de gestión de paradas no se limita a los informes. Las rutinas de seguimiento de tiempos de inactividad de equipos y SIC incorporadas, con el apoyo de expertos operativos internos, guiarán a tu equipo para reducir los tiempos de inactividad no planificados.
Hacer un seguimiento del tiempo de inactividad es bueno. Detectar automáticamente la Pérdida Causal Verdadera es mejor.
Un mejor seguimiento del tiempo de inactividad de los equipos es sólo el primer paso para una mejor supervisión y gestión del tiempo de inactividad OEE. El algoritmo inteligente de Pérdida Casual Verdadera de LineView correlaciona automáticamente una avería a nivel de máquina con el impacto en esa máquina y tu puntuación de Eficiencia General del Equipo (OEE). La categorización adicional del tiempo de inactividad en las seis pérdidas de OEE proporciona una imagen precisa del tiempo de inactividad y de las acciones prioritarias. Al cambiar el enfoque de los tiempos de inactividad de la máquina a las Pérdidas Causales, los equipos de mejora continua y los operarios pueden alejarse de las intervenciones reactivas que son perjudiciales e ineficaces.
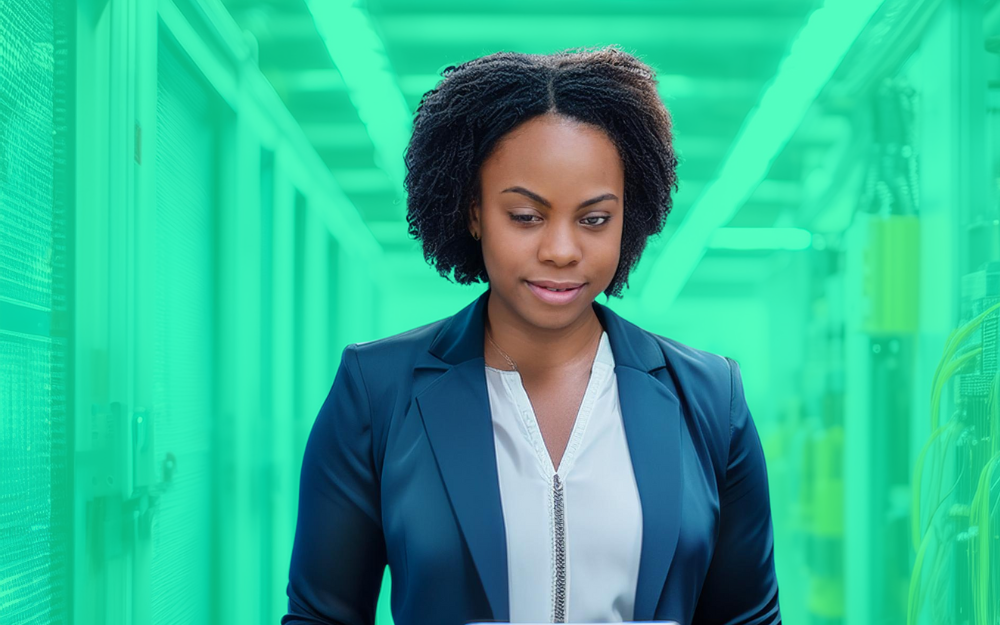
Cómo funciona el seguimiento del tiempo de inactividad:
1. Utiliza el software de LineView para realizar un seguimiento preciso del tiempo de inactividad de los equipos
Actualizar el seguimiento automatizado del tiempo de inactividad de las máquinas y la detección automática de averías no sólo mejora la supervisión de la producción, sino que también proporciona a los operarios y directivos información precisa y procesable, no suposiciones.
2. Detecta automáticamente las verdaderas causas del tiempo de inactividad para reparaciones más eficaces
Conocer la causa subyacente del tiempo de inactividad permite a los equipos reparar la limitación de la línea en lugar de los síntomas aguas arriba o aguas abajo.Los equipos Ahorrarán tiempo y mano de obra perdidos, lo que beneficiará a tu cuenta de resultados de rentabilidad.
3. Optimiza el tiempo de gestión y la productividad de los trabajadores
El uso de la función automatizada de seguimiento de los tiempos de inactividad ocasionales de las máquinas de LineView libera tiempo de gestión para centrarse en la formación y las mejoras de los procesos. Facilitar a los directivos las causas raíz de los fallos de las máquinas ahorra horas de análisis e informes históricos.
4. Acelera los cambios y agiliza la planificación del mantenimiento
Una vez que tu equipo haya atacado las mayores fuentes de paradas crónicas e intermitentes, aplica los datos y herramientas de LineView a los cambios, las actividades de mantenimiento planificadas y otras mejoras enfocadas.
Un tiempo de inactividad cero y una mejora de la OEE del 10% son más fáciles con la pérdida causal.
En lugar de centrarte en incidentes individuales de tiempo de inactividad, LineView te ayuda a ir más allá de los síntomas para llegar a la verdadera causa del tiempo de inactividad.
La mejora de la OEE, la supervisión del tiempo de inactividad de las microparadas, el análisis automático de averías y las herramientas de productividad son las herramientas que tu equipo necesita para una reducción sostenible del tiempo de inactividad. ¿Y como extra? Consigue una mejora de la eficiencia garantizada del 10%.
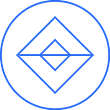
Be proactive to prevent machine downtime
Ganancias mínimas del 10% en OEE
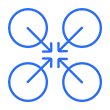
Go beyond symptoms to true causes of downtime
Cambios más rápidos
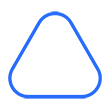
Get accurate unplanned equipment downtime statistics
Reduce (o elimina) las costosas microparadas
Historias de clientes
Sumérgete en cómo Lineview ayuda a los fabricantes a transformar la producción. Creemos que el éxito es una calle de doble sentido (win-win), así que explora cómo nuestros clientes ganan a lo grande, y cómo su éxito alimenta nuestro impulso para seguir innovando.
Caso práctico
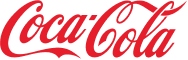
Coca-Cola Enterprises selects Lineview™ as their system of choice.
Durante un periodo de tres años, LineView™ se ha implantado en todas las líneas de producción de Europa para ayudar a aumentar la eficacia y reducir los costes de fabricación.
Caso práctico

AB InBev China achieves Goals through Data, focus and action.
La mayor cervecera del mundo, AB InBev, recomendó LineView™ a su planta de embotellado china con sede en Wuhan para remediar los problemas de eficacia de la empresa.
Caso práctico
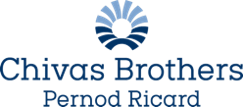
Chivas Brothers Pernod Ricard increases mechanical efficiency by 17% in six months.
La eficacia mecánica de la línea 33 aumentó del 60% al 70% tras seis meses de intervenciones basadas en datos y mejoras focalizadas.