Lean y Mejora Continua
Elimina los residuos mediante la fabricación ajustada y permite la mejora continua.
¿Cuál es la diferencia entre la fabricación ajustada y la mejora continua?
Pasarse al pensamiento ajustado crea una actitud totalmente nueva en toda la organización. Tendrá numerosos efectos positivos y generará un impulso positivo en toda la empresa.
Se trata de un conjunto de herramientas y metodología de fabricación ajustada guiadas por los principios de la fabricación ajustada, cuyo énfasis principal es la eliminación de los residuos, en particular las actividades sin valor añadido (NVA), es decir, las que requieren tiempo y/o recursos, pero no añaden valor al cliente.
La mejora continua en la fabricación ajustada desafía el statu quo y plantea la pregunta: ¿hay una forma mejor? En otras palabras, alcanzar la perfección.
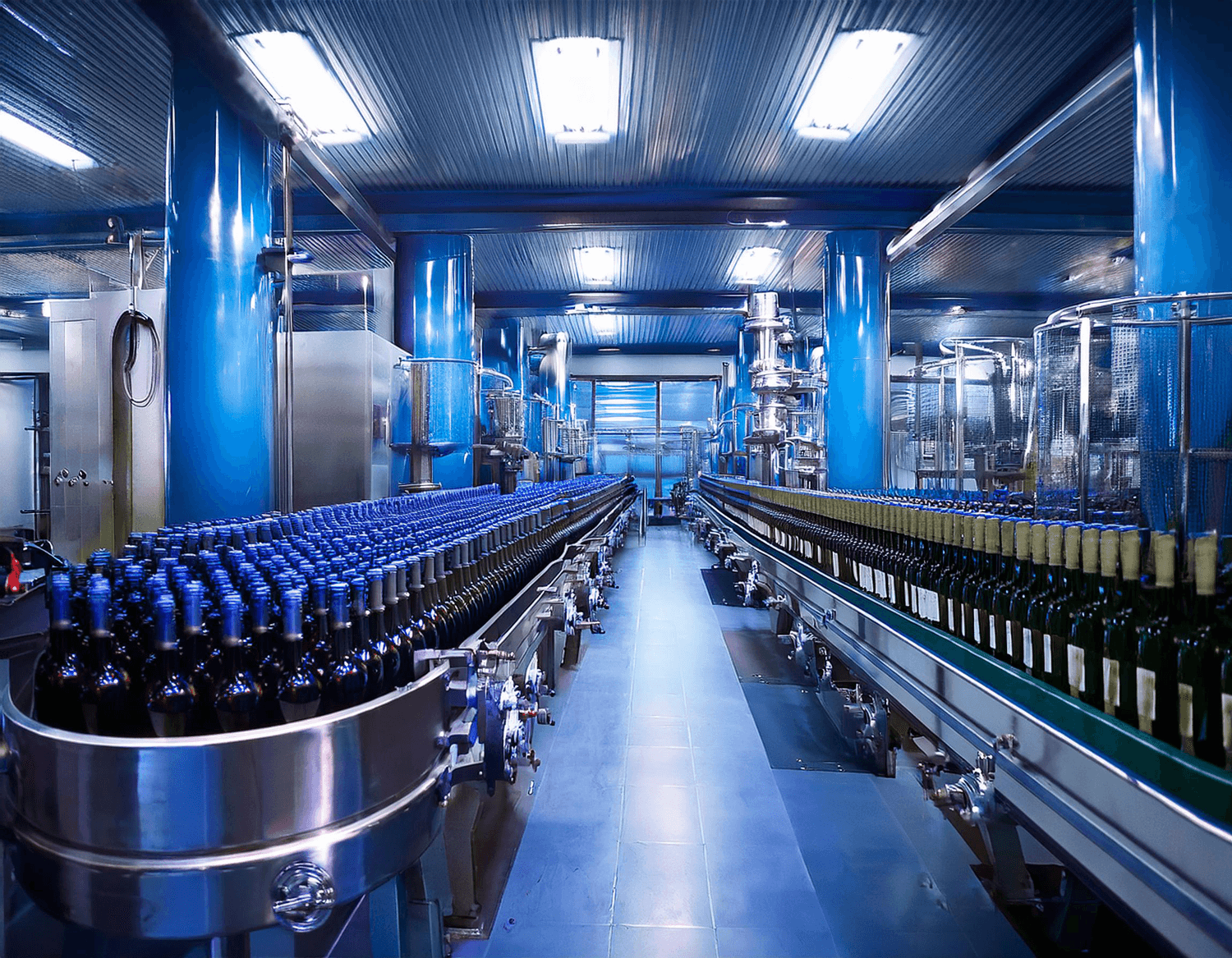
¿Cómo pueden colaborar la fabricación ajustada y las iniciativas de mejora continua?
Imagina a todo el equipo del taller sintonizado para identificar y eliminar los residuos. Desde el principio de cada turno, todos los empleados -desde los operarios, pasando por la dirección, hasta el personal de oficina- adoptan una cultura de mejora continua en la fabricación, y buscan formas de hacer que su proceso sea más ágil y eficiente.
Esto es tanto pensamiento ajustado como mejora continua.
Entonces, ¿cuál es la diferencia entre la fabricación ajustada y la mejora continua? Lo cierto es que van juntas, de la mano.
Una planta que adopte la fabricación ajustada también adoptará la mejora continua. Al eliminar los residuos, se aumenta la OEE y se mejora el proceso de fabricación.
Pensamiento Kaizen para la Mejora Lean de Procesos
Kaizen es un principio fundamental para la mejora continua en la fabricación. En japonés significa cambiar para mejorar, y es famoso por ser uno de los principios fundamentales del Sistema de Producción Toyota. En esencia, es un enfoque a largo plazo y una filosofía de fabricación que se centra en:
- eliminar los residuos
- mejorar la productividad
- mejora continua sostenida y orientada
Kaizen implica que los pequeños cambios incrementales aplicados rutinariamente a lo largo del tiempo darán lugar a oportunidades de mejora significativas.
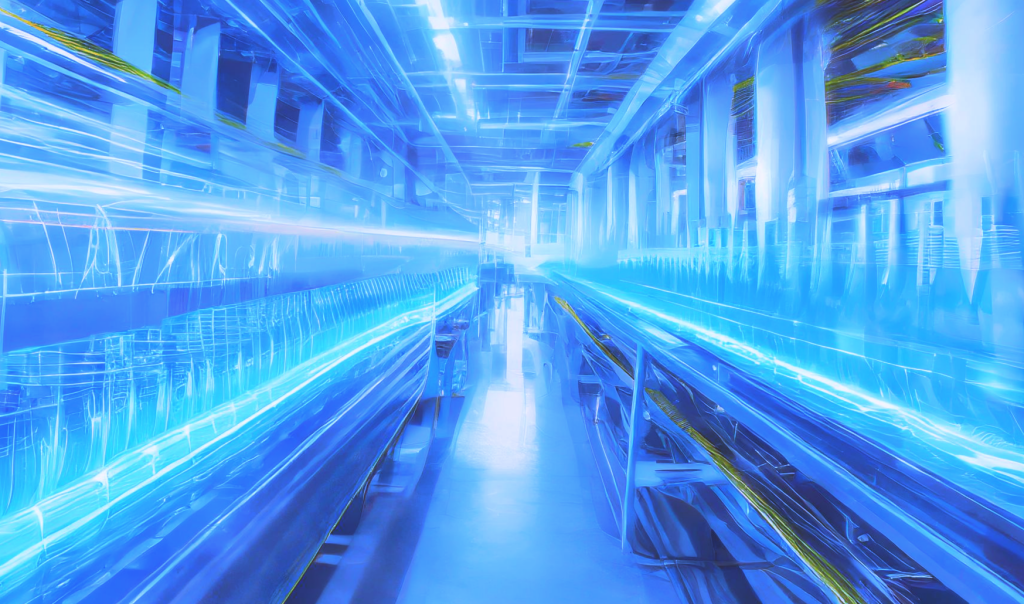
Impulsores clave de la mejora continua ajustada en la fabricación
Todas las plantas de fabricación deberían adoptar la mejora continua ajustada. No importa el volumen de producción, el número de empleados o la complejidad de la operación, los principios de mejora continua lean eliminarán sin duda los despilfarros.
La mejora continua Lean es un proceso de mejora sistémico, rutinario y cíclico que profundizará en los puntos débiles de cualquier proceso de fabricación.
Con operarios y jefes de planta sintonizados para identificar activamente los residuos, y tomar medidas rápidas sobre cómo eliminarlos, aumentará la eficiencia, lo que dará a las plantas una ventaja competitiva significativa.
El factor clave para que tu planta desarrolle la fabricación ajustada y una estrategia de mejora continua es el hecho de que ninguna planta es perfecta, y casi todos los procesos de producción pueden mejorarse.
La mentalidad de la mejora continua ajustada en la fabricación:
¿La mejora continua ajustada en la fabricación es una estrategia? No… es una mentalidad.
La mejora continua Lean es más que una casilla de verificación, es más que hojas de cálculo o algunos garabatos en una pizarra.
El enfoque de fabricación ajustada y mejora continua debe adoptarse en toda la planta. Es una fuerza motriz para hacerlo mejor, y para que los turnos sean más eficientes y, en última instancia, más satisfactorios para los operarios y los jefes de planta.
En lugar de evitar los problemas en la planta, ¿por qué no trabajar para solucionarlos? La práctica de la mejora continua en la fabricación ajustada permite una mejora incremental, lo que significa que los problemas pueden resolverse con el tiempo.
Eliminar estos puntos conflictivos y baches a lo largo del proceso de fabricación sin duda mejora la eficacia y elimina procesos de trabajo inútiles, pero también alivia las frustraciones y hace que la jornada laboral sea más fluida para los empleados del taller.
Proceso totalmente guiado
Audit data, methodology and line balancing software, all in one
No es sólo un software de equilibrado de líneas de producción, nuestro equipo proporciona un cambio de paso garantizado en el equilibrado de líneas de fabricación. Te guiaremos a través de una auditoría basada en datos, implantaremos cinco niveles de control y formaremos a tu equipo para que utilice el software de equilibrado de líneas de LineView, todo ello para obtener resultados a largo plazo.
Evaluación comparativa integrada
Line balance scores make benchmarking easy
Facilitar el equilibrado de la línea de producción es la clave para obtener resultados duraderos. El software de equilibrado de líneas LineView incorpora puntuaciones de equilibrado de líneas de producción fáciles de entender para cada tipo de producto, con comparaciones de referencia integradas. Los equipos pueden comparar los datos en tiempo real con los históricos, para que nunca pierdas tus ganancias de capacidad.
Aumento adicional del rendimiento
Optional controls to automate restarts and recover speed
El control opcional del equilibrio de la línea de fabricación desbloquea ganancias de rendimiento adicionales de entre el 2 y el 5%. Este módulo de control supervisor de la línea establece tiempos óptimos de reinicio en las máquinas principales (llenadora, etiquetadora, empaquetadora) para acelerar la recuperación tras un tiempo de inactividad.
¿Qué es Lean?
Beneficios del Lean
La fabricación ajustada y la mentalidad lean mejoran la eficiencia de la planta, reducen los residuos y aumentan la productividad.
Adoptar soluciones de fabricación ajustada en todo el taller conducirá a un aumento de la OEE, ya que cada una de las seis pérdidas se reducirá sistemáticamente.
A medida que mejore el proceso y se optimice la producción, los operarios podrán centrarse en su trabajo, y no en los problemas que frenan la producción. Además, dar más responsabilidad y confianza a los operarios y jefes de planta para identificar los problemas hará que sus turnos tengan más sentido.
Desde el punto de vista de la sostenibilidad, la fabricación ajustada es la forma original de ser ecológico. Al eliminar los residuos mediante la producción ajustada, tu planta estará mejor preparada para cumplir unos requisitos medioambientales y de sostenibilidad cada vez más estrictos.
Conceptos erróneos sobre Lean
Para ser un concepto que existe desde hace casi 100 años, hay muchos mitos y conceptos erróneos sobre Lean en la fabricación. Para la industria manufacturera, los tres principales conceptos erróneos son:
- Mito: El Lean acaba con los puestos de trabajo. Realidad: Lean sólo optimiza los puestos de trabajo y hace que los procesos funcionen con más fluidez, con menos residuos. Los operarios tienen más tiempo para centrarse en su verdadero trabajo, aumentar la producción y aumentar la eficacia.
- Mito: La implantación del Lean es cara. Realidad: ¡La mentalidad lean es gratis! Por supuesto, la formación y algunos programas son necesarios. Pero adoptar el lean y formar al personal de toda la empresa puede ser barato con la estrategia adecuada. Al final, el lean ahorrará dinero gracias a la eliminación de residuos.
- Mito: Lean requiere fórmulas, diagramas de flujo y procesos complicados. Realidad: Lean es sencillo: los pequeños cambios incrementales impulsan la mejora continua y la eliminación de residuos. A menudo, metodologías como Seis Sigma se combinan con el lean, y requieren una estrategia y un análisis un poco más complejos. Pero la fabricación ajustada y la mentalidad ajustada no requieren técnicas complejas como Seis Sigma.
Fundamentos de los procesos de mejora continua de la fabricación ajustada
En toda la industria manufacturera se han definido procesos lean generales para establecer métricas que permitan evaluar el impacto del lean.
Los llamamos los Cinco Principios de la Mejora Continua Lean en la Fabricación.
¿Cuáles son los cinco principios de la fabricación ajustada?
1. Valor
La determinación de qué características crean valor en un producto se hace tanto desde el punto de vista del cliente interno como del externo. El valor se expresa en términos de cómo el producto o servicio concreto satisface las necesidades de los clientes, en un momento concreto o a un precio concreto.
2. Flujo de valor
La secuencia completa de actividades en todas las partes de la organización implicadas en la entrega del producto o servicio. Representa el proceso integral que aporta valor al cliente. Estas actividades pueden ser de Valor Añadido o de No Valor Añadido.
Actividades de Valor Añadido: Actividad que transforma o da forma (por primera vez) a material o información para satisfacer el valor del cliente.
Actividades sin Valor Añadido: Actividades que no aportan valor al producto o servicio (desde el punto de vista del cliente). Al definir claramente el Valor de un producto o servicio concreto desde la perspectiva del cliente final, todas las actividades que no aportan valor pueden ser objeto de eliminación.
3. Flujo
El flujo es el movimiento ininterrumpido del producto o servicio a través del sistema hasta el cliente. Una vez identificadas y eliminadas del proceso las actividades sin valor añadido (residuos), el producto o servicio fluirá a través de las actividades con valor añadido y hacia el cliente.
4. Tira de
Pull consiste en comprender la demanda del cliente sobre tu servicio y luego crear tu proceso para responder a ella. Un sistema pull te ayudará a producir sólo lo que el cliente quiere, cuando el cliente lo quiere.
5. Perfección
El flujo y el tirón se crean y establecen, pero no se detienen ahí. La mejora continua Lean te permite esforzarte continuamente por eliminar las actividades sin valor añadido, mejorar el flujo y maximizar la satisfacción del cliente.
Aunque la mejora continua en la fabricación ajustada se centra en la eliminación de residuos, la mejora del flujo y la mejora continua, también tiene otras ventajas. Se mejora la calidad. El producto pasa menos tiempo en proceso, lo que reduce las posibilidades de daños u obsolescencia. La simplificación de los procesos da lugar a una reducción de la variación. A medida que la organización examina todas las actividades del flujo de valor (mediante el mapeo del flujo de valor), se elimina la restricción del sistema y se mejora el rendimiento.
La fabricación ajustada y la mejora continua implican a muchas personas en el flujo de valor. La transición al pensamiento de flujo provoca grandes cambios en la forma en que las personas perciben sus funciones en la organización y su relación con el producto.
La organización debe estar preparada para aceptar y afrontar el cambio y comprender que cada persona asumirá el cambio a un ritmo diferente.
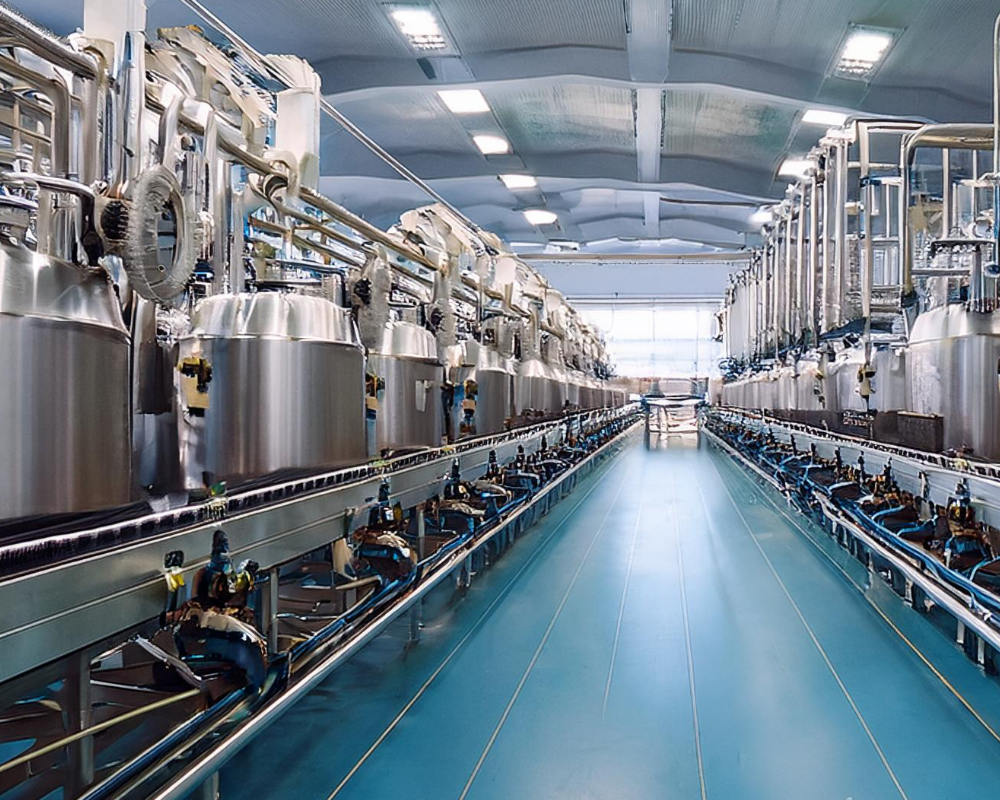
¿Qué es la Mejora Continua en la Fabricación?
Modelo de Mejora Continua en la Fabricación
El Modelo de Mejora Continua (IC) es un marco que ayuda a identificar, analizar y optimizar los procesos mediante iniciativas de mejora continua. El Modelo de Mejora Continua es un proceso iterativo: existen cuatro principios fundamentales de la IC.
¿Cuáles son los 4 principios de la IC?
Planificar – Hacer – Comprobar – Actuar
Planificar: Establecer objetivos de mejora de procesos específicos o globales basados en el estado actual
Hacer: Realizar el trabajo necesario para cumplir esos objetivos
Comprobar: Realiza pruebas con el método para validar y analizar los resultados de forma continua.
Actúa: Pon en marcha la mejora del proceso. Controla de cerca los resultados. Si es posible mejorar aún más el proceso, repite el ciclo Planificar-Hacer-Verificar-Actuar para eliminar aún más los residuos, reducir las ineficiencias y mejorar las operaciones.
Los datos históricos y en tiempo real de cada proceso son muy valiosos en todo el Modelo de IC para desglosar los resultados y tener una visión holística de la iniciativa de mejora.
Metodologías de MejoraContinua de la Fabricación
Junto con los cuatro principios de la IC, hay ciertas metodologías útiles que pueden mejorar los esfuerzos de mejora continua en el taller.
Análisis de la causa raíz
Cuando se produce un problema, es esencial entender por qué. Al emprender la mejora continua en la fabricación, llegar a la causa raíz de cualquier problema es el primer paso para arreglar un proceso roto.
Hay varias formas de realizar un análisis detallado de la causa raíz. Las soluciones digitales que se conectan directamente al taller pueden ofrecer una visibilidad total y proporcionar a los operarios, jefes de planta y altos directivos los mejores datos para llegar a las causas raíz de cada problema.
Lean Kanban
Si has trabajado en una empresa lean, Kanban puede resultarte familiar aunque nunca hayas oído el término. Puede que hayas visto grandes pizarras blancas con notas post-it (o tableros Kanban), pegatinas y flechas.
En esencia, Kanban es un método de gestión del flujo de trabajo ajustado. Es una forma de visualizar los proyectos lean y de mejora continua mediante el uso de gráficos y diagramas fáciles de leer y comprender.
Kanban es eficaz para ayudar a los equipos a ver un camino directo y claro hacia el flujo de trabajo del proyecto para ayudar a la mejora del proceso.
Lean Six Sigma
Six Sigma es un conjunto de técnicas y herramientas estadísticas y basadas en datos en el contexto de Lean que pueden ayudar a identificar y minimizar errores y defectos.
Es un proceso detallado de control de calidad que sólo permite 6 desviaciones estándar (6σ) entre la media y los límites aceptables para reducir los defectos de fabricación a no más de 3,4 ocurrencias por millón de unidades o eventos.
Seis Sigma es un potente enfoque científico que puede utilizarse dentro del marco Lean, pero, como ya se ha dicho, implica especialización y análisis más complejos.
Límites WIP
Los límites WIP (Trabajo en curso) son restricciones sobre cuántos elementos se están trabajando activamente en un momento dado. En términos de Mejora Continua en la fabricación, esto podría significar cuántos procesos está intentando mejorar activamente cada trabajador o equipo individual utilizando el modelo de Mejora Continua de la Fabricación.
Los límites de trabajo en curso ayudan a reducir el riesgo y a mantener las iniciativas de IC bajo control, sin abrumar a los miembros del equipo con demasiados proyectos en curso.
Cómo maximizar el valor con la Mejora Continua Lean
Adoptar la digitalización con la fabricación ajustada y la Mejora Continua
En Lineview, nos apasiona crear plantas preparadas para el futuro y ágiles en un panorama de fabricación cada vez más digital.
Integrar la tecnología punta y la digitalización no significa que se puedan ignorar los principios de la mejora continua ajustada en la fabricación. Más bien al contrario.
A medida que los talleres se vuelven más digitales, más autónomos y más conectados, la mentalidad lean de mejora continua permitirá a los talleres sobresalir en su búsqueda de la eliminación del despilfarro.
Afronta tus residuos adoptando la filosofía de fabricación continua ajustada. Apúntate a una auditoría operativa gratuita o a la Academia Lineview para que podamos ayudar a tus equipos operativos a aprovechar el verdadero poder del lean.
Un tiempo de inactividad cero y una mejora de la OEE del 10% son más fáciles con la pérdida causal.
En lugar de centrarte en incidentes individuales de tiempo de inactividad, LineView te ayuda a ir más allá de los síntomas para llegar a la verdadera causa del tiempo de inactividad.
La mejora de la OEE, la supervisión del tiempo de inactividad de las microparadas, el análisis automático de averías y las herramientas de productividad son las herramientas que tu equipo necesita para una reducción sostenible del tiempo de inactividad. ¿Y como extra? Consigue una mejora de la eficiencia garantizada del 10%.
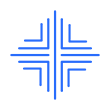
Be proactive to prevent machine downtime
Ganancias mínimas del 10% en OEE
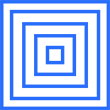
Go beyond symptoms to true causes of downtime
Cambios más rápidos
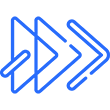
Get accurate unplanned equipment downtime statistics
Reduce (o elimina) las costosas microparadas
Historias de clientes
Sumérgete en cómo Lineview ayuda a los fabricantes a transformar la producción. Creemos que el éxito es una calle de doble sentido (win-win), así que explora cómo nuestros clientes ganan a lo grande, y cómo su éxito alimenta nuestro impulso para seguir innovando.
Caso práctico
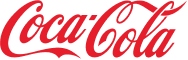
Coca-Cola Enterprises selects Lineview™ as their system of choice.
Durante un periodo de tres años, LineView™ se ha implantado en todas las líneas de producción de Europa para ayudar a aumentar la eficacia y reducir los costes de fabricación.
Caso práctico

AB InBev China achieves Goals through Data, focus and action.
La mayor cervecera del mundo, AB InBev, recomendó LineView™ a su planta de embotellado china con sede en Wuhan para remediar los problemas de eficacia de la empresa.
Caso práctico
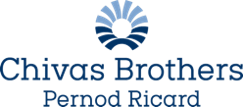
Chivas Brothers Pernod Ricard increases mechanical efficiency by 17% in six months.
La eficacia mecánica de la línea 33 aumentó del 60% al 70% tras seis meses de intervenciones basadas en datos y mejoras focalizadas.