Embrace digital. Pit stop your manufacturing and accelerate.
Complete Digital Transformation for your manufacturing
Don’t settle for the status quo. Unlock your full potential. Our digital solutions empower you to achieve peak performance, optimize production, streamline operations, and embrace sustainable practices.
Together, we’ll unlock a future of efficiency, environmental responsibility and a happier workplace.
Lineview™
Lineview is our cutting-edge platform designed to tackle the complex challenges of manufacturing and transform your production to a real-time symphony of efficiency.
With Lineview, on-time delivery, efficient management of fluctuating demand, and minimized waste becomes the norm. Lineview helps you navigate the dynamic world of production by providing a powerful and clear view of your resources, allowing you to make informed decisions and achieve peak production efficiency.
Key benefits
- Data and AI driven targeted actionable insights
- Seamless integration into existing ERP and MES solutions.
- Automated true causal loss and production monitoring
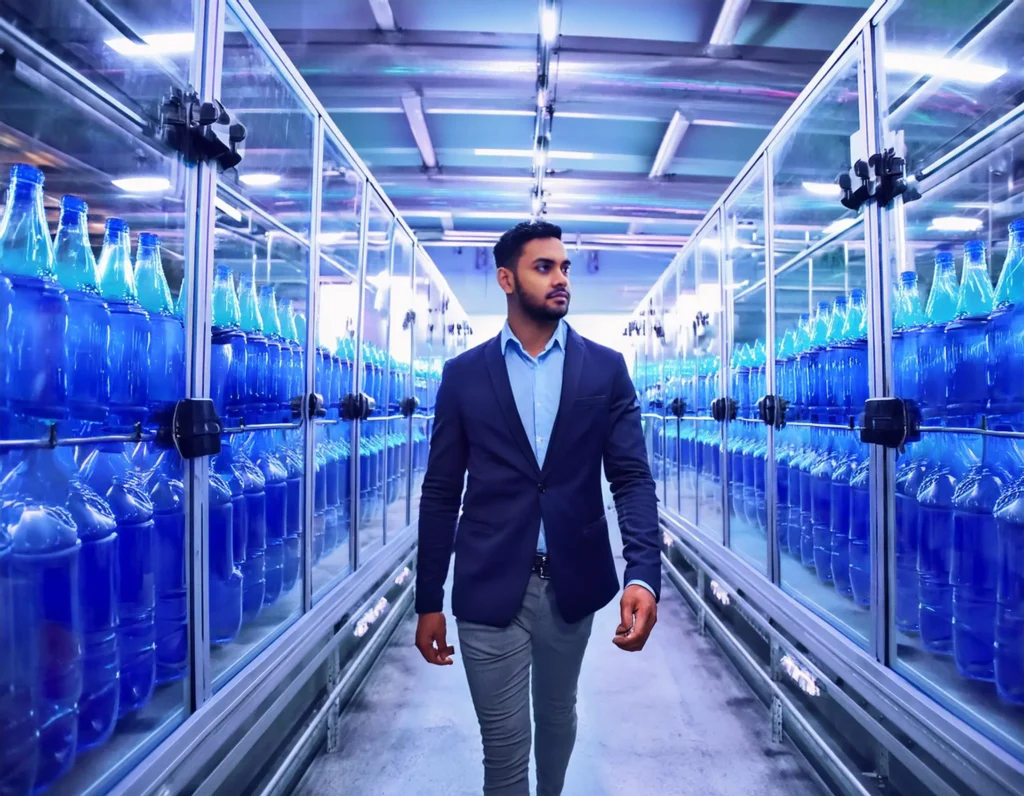
XL Platform
The Solution for bolt-on productivity improvement. Stop downtime in its tracks! XL Platform transforms your plant into a data-driven powerhouse. This easy-to-install solution eliminates downtime guesswork with real-time tracking. Gain crystal-clear visualizations of production, empower your workforce to identify bottlenecks and optimize every step for peak efficiency. Win every minute & every shift with automated production monitoring.
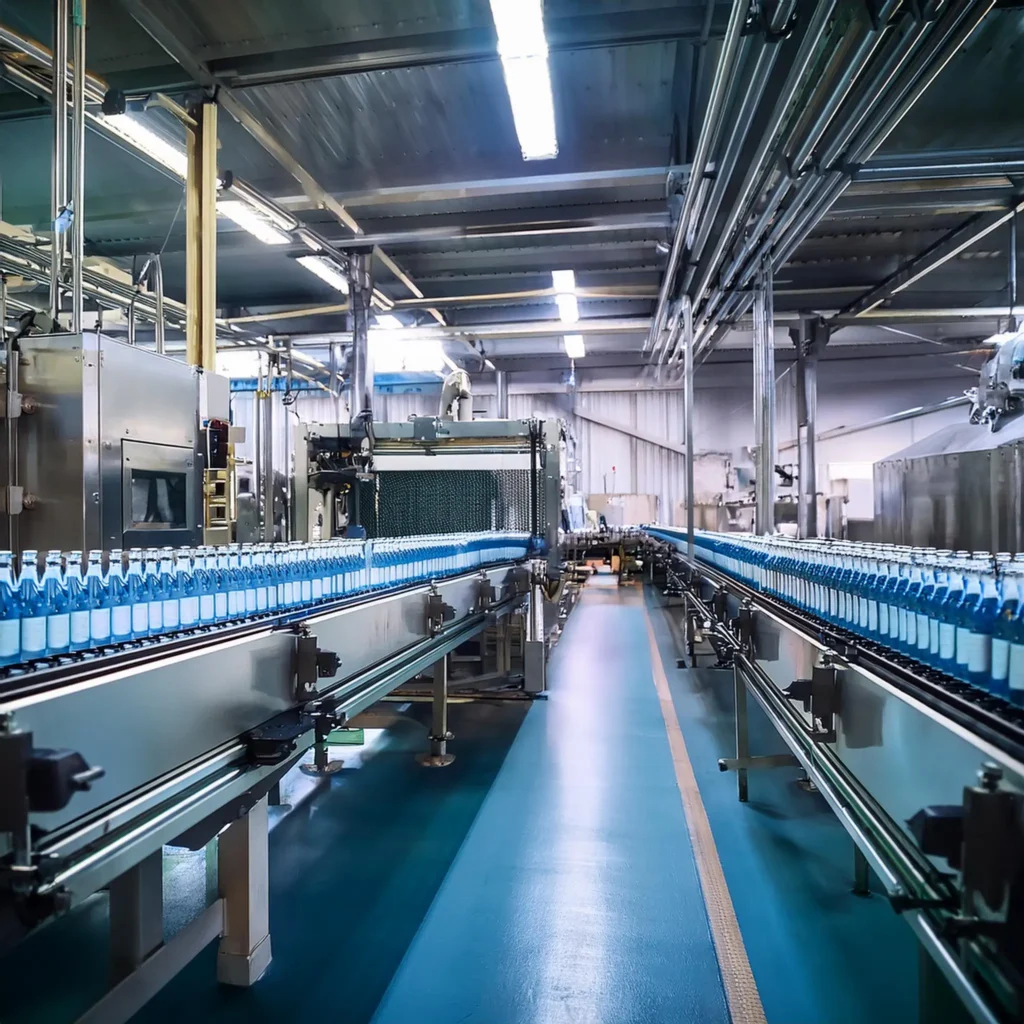
DigiView
Ensure top quality in production. DigiView transforms all production checks from laborious spreadsheets or paper-based process into a digital Industry 4.0 ready process. Uncover real-time insights across shifts, empowering smarter decisions and optimized workflows for the entire enterprise. DigiView helps you adhere to the highest quality standards in production.
Key benefits
- Automated quality management
- Paperless manufacturing operations
- Flexible for any check or processes
RapidView
RapidView boosts productivity with real-time insights. Visualize cycle time, capture data wirelessly, and drill down into performance gaps. Track maintenance KPIs, analyse losses, and access configurable reports. RapidView is ideal for regular equipment audits to justify CapEx and enables continuous improvement initiatives to resolve bottlenecks rapidly. Plus, explore add-on modules for enhanced capabilities.
Key benefits
- Zero impact – independent of existing infrastructure
- Built-in tactical reporting
- Wireless data capture via battery- powered sensors
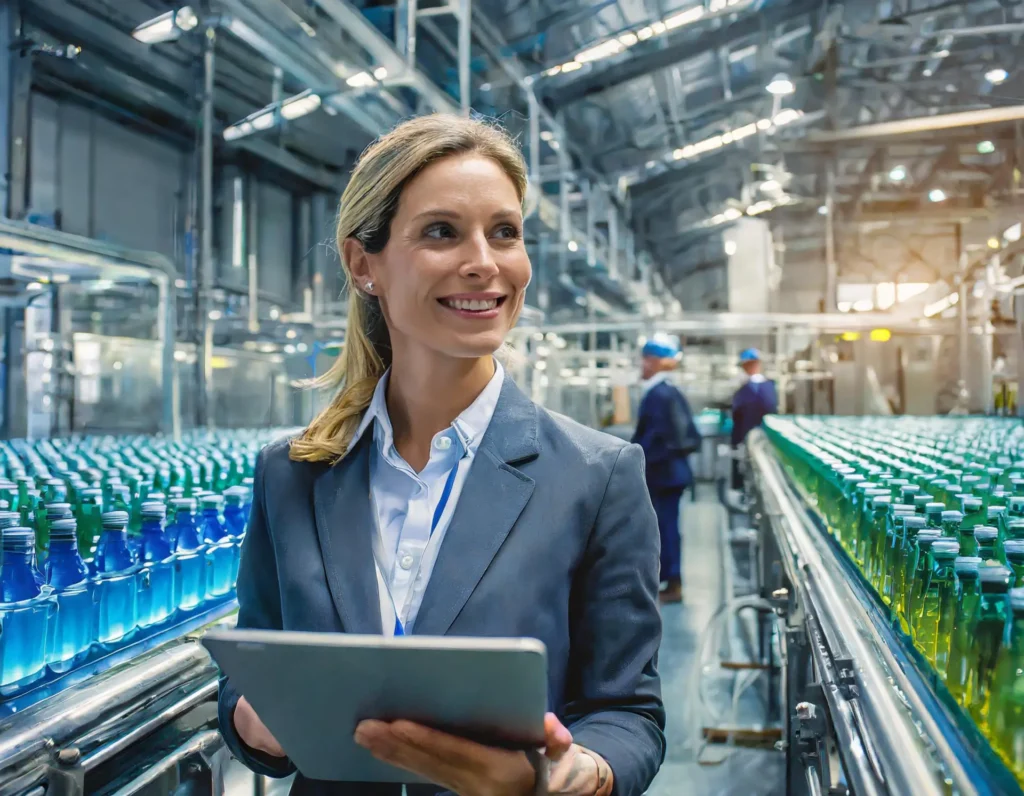
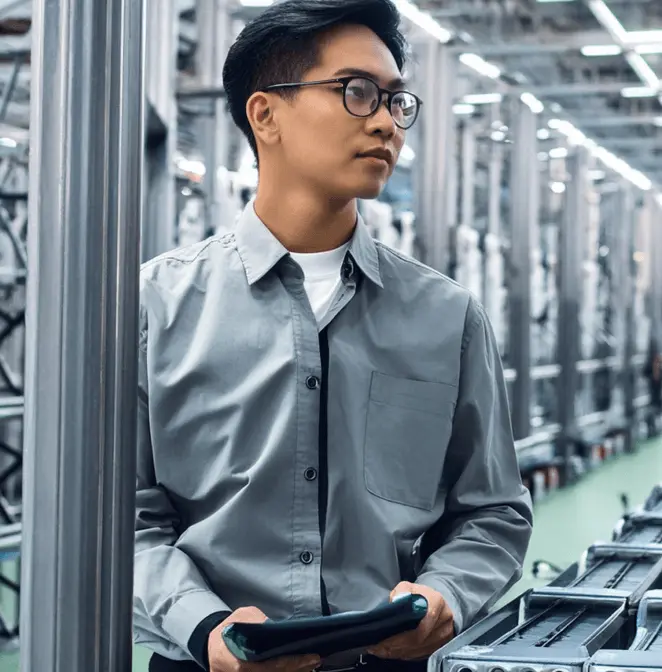
MachineView
Gain real-time, machine-level insights to proactively address issues and optimize production. MachineView goes beyond simply monitoring – it tracks key metrics like MTBF and MTTR, empowering you to make data-driven decisions that minimize downtime and maximize output. Identify bottlenecks, reduce waste, and achieve operational excellence with MachineView’s actionable drill-down analytics.
Key benefits
- Drive effective decisions with 6-Loss detailed analysis.
- Gain reject insight with real-time reject monitoring and minimize lost output.
- Enable company-wide access at no additional cost with unlimited user licenses.
Customer stories
Dive into how Lineview empowers manufacturers to transform production. We believe success is a two-way street, so explore how our customers win big, and how their success fuels our drive to keep innovating.
Case Study
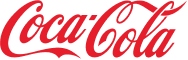
Coca-Cola Enterprises selects Lineview™ as their system of choice.
Over a three-year period, Lineview™ has been implemented on every production line in Europe to help increase efficiency and reduce manufacturing costs.
Case Study

AB InBev China achieves Goals through Data, focus and action.
The world’s largest brewer, AB InBev, recommended Lineview™ to their Chinese bottling plant based in Wuhan to remedy the company’s struggles with efficiencies.
Case Study
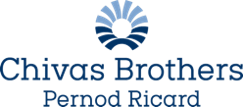
Chivas Brothers Pernod Ricard increases mechanical efficiency by 17% in six months.
Line 33’s Mechanical Efficiency increased from 60% to 70% after six months of data-driven interventions and focused improvements.