What are Andon systems or Andon lamps?
Andon lamps are an extremely simple system of visual factory management for helping teams identify when there is a problem with a process or machine. Originally they were developed as part of the Jidoka quality-control method within the Toyota Production System and have now been incorporated into standard lean manufacturing practice
Originally andon lamps were used to notify teams of a quality problem, and more frequently we see them installed on continuous flow lines to help inform operators of why machines have stopped. For example if i have an operator running two packaging machines and one of the machines stop, a simple Andon light stack can instantly tell the operator if he has a problem (and has to intervene) or if the machine has just run out of product.
Here is a sample Andon System, and there are more courtesy of google images:
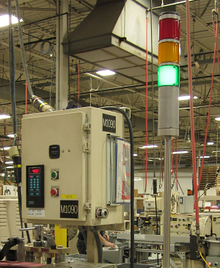
Benefits of traditional Andon systems in your visual factory:
- Reduce reaction times for machine problems – operators see the state of machines quickly
- Reduced downtime for fault fixing – lamps indicate most common “faults” e.g. low reel, jams etc
- Improve management efficiency – Managers can quickly see which machines are stopped on a busy floor
Drawbacks of traditional Andon systems in your lean implementation:
- Signals need to be interpreted – complex systems need a code or key card to help operators remember what the alarms mean.
- Can be hard to see – if they’ve been in place for a long time lights often get damaged and dirty and can be hard to see. They can also often become ‘background noise’.
Taking Andon systems to the next level…XL800 for the ultimate visual factory
The XL800 OEE system brings Andon systems into the 21st century by taking all the strengths of existing systems, adding even more functionality, whilst keeping the core simplicity.
When you install an XL800 OEE System on your machine or line the highly visual alphanumeric display system can be used to highlight KPI’s and running conditions just like any display system.
Basic functionality:
Almost instantly the XL800 OEE system can support your lean manufacturing implementation by very quickly enabling you to show:
- MACHINE DOWN + Duration of downtime
- BREAK TIME REMAINING + Duration of break
- CHANGEOVER + Duration of changeover
More advanced functionality:
If you can get a signal from your machine to indicate why that machine has stopped then your XL800 could automatically display additional faults or alarms such as:
- Stop – Build Back (too much product on outfeed)
- Stop – Lack (no raw materials on infeed)
- Stop – No raw material
- Stop – Guards open
- Quality check due now (based on the number parts produced)
- Stop – SPECIFIC FAULT MESSAGE
- Target achieved – Good job team
- …..and the list goes on! If you can get us a signal, the XL800 OEE System can give you a display!
So what are the benefits of an XL800 as your Andon system?
- All of the benefits as traditional Andon systems
- Inform and motivate your team: by displaying real time data for how long each alarm has been triggered, and by showing targets for the production run
- Increase productivity: Simplify your shop floor – the display is 100% user configurable so you can quickly select the alarms that make the most difference to you
- Save money: Your operators will be able to respond to the right causes of machine downtime with machine downtime tracking software and get your machines fixed faster.
- Increase OEE: With machines being fixed faster you will produce more product than ever before
- Essential for TPM: The built in reporting and analytics software in the XL800 system is ideal for driving your TPM implementation as part of your lean journey.