Lean and Continuous Improvement
Eliminate waste through lean manufacturing and enable continuous improvement.
What’s the Difference Between Lean Manufacturing and Continuous Improvement?
Making a move to lean thinking creates an entirely new attitude throughout the entire organisation. It will result in numerous positive impacts and generate positive momentum across the shop floor.
A set of lean manufacturing tools and methodology guided by lean principles, the key emphasis in lean manufacturing is the elimination of waste, particularly Non-Value Added (NVA) activities – those that take time and/or resources, but do not add to the customer value.
Continuous improvement in lean manufacturing challenges the status quo and asks the question: is there a better way? In other words, reaching for perfection.
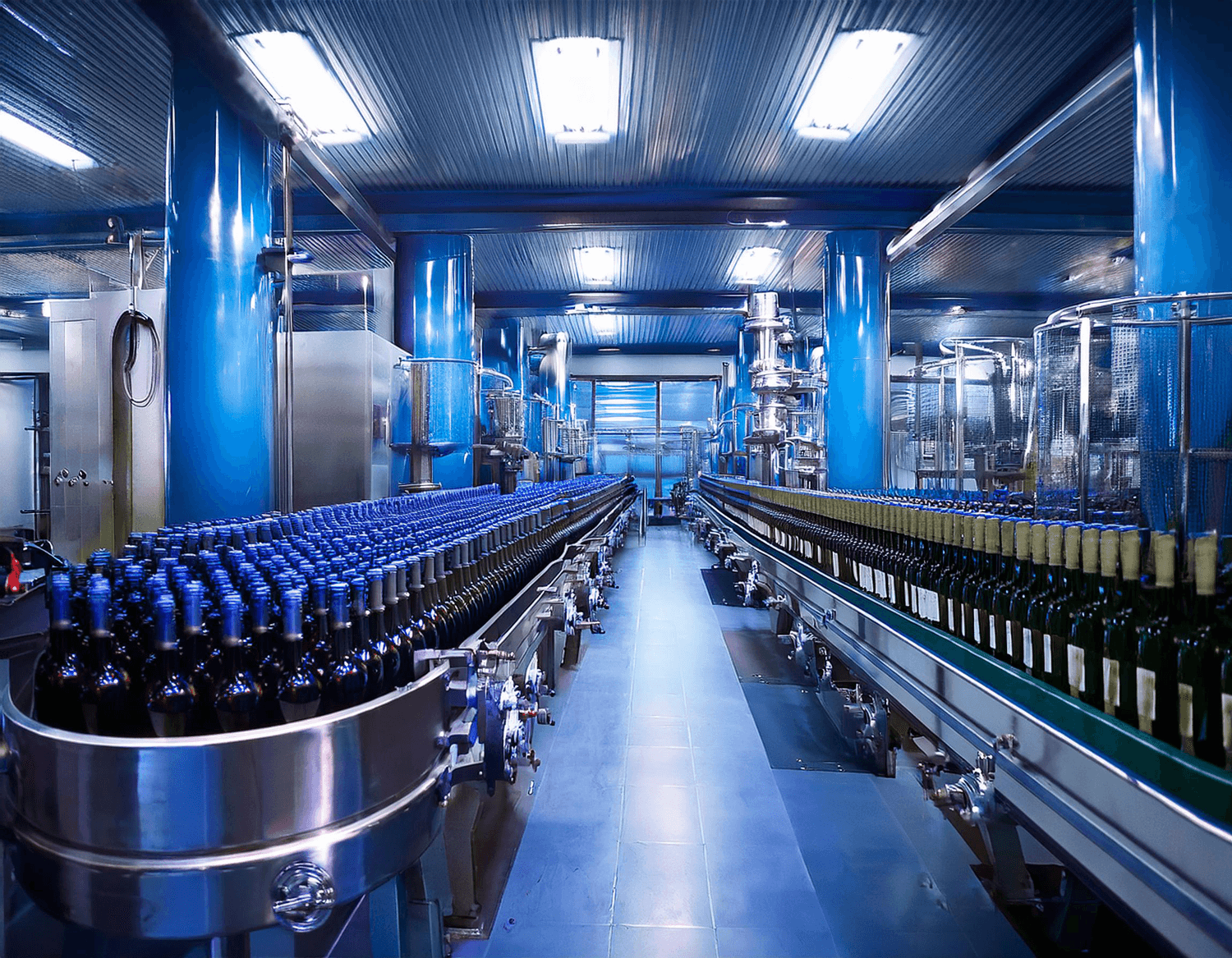
How Can Lean Manufacturing and Continuous Improvement Initiatives Work Together?
Imagine the entire shop floor team tuned-in to identify and eliminate waste. From the start of each shift, every employee – from operators, to leadership, to office staff – embrace a culture of continuous improvement in manufacturing, and look for ways to make their process more streamlined and efficient.
This is both lean thinking and continuous improvement.
So, what is the difference between lean manufacturing and continuous improvement? The fact is that they go together, hand-in-hand.
A plant who embraces lean manufacturing will also embrace continuous improvement. Through eliminating waste, OEE is boosted and the manufacturing process is improved.
Kaizen Thinking for Lean Process Improvement
Kaizen is a foundational principle for lean and continuous improvement in manufacturing. Japanese for change for better, Kaizen is famously one of the main principles of The Toyota Production System. At the core, it’s a long-term approach and manufacturing philosophy that focuses on:
- eliminating waste
- improving productivity
- sustained targeted continual improvement
Kaizen implies that incremental, small changes routinely applied over time will result in significant improvement opportunities.
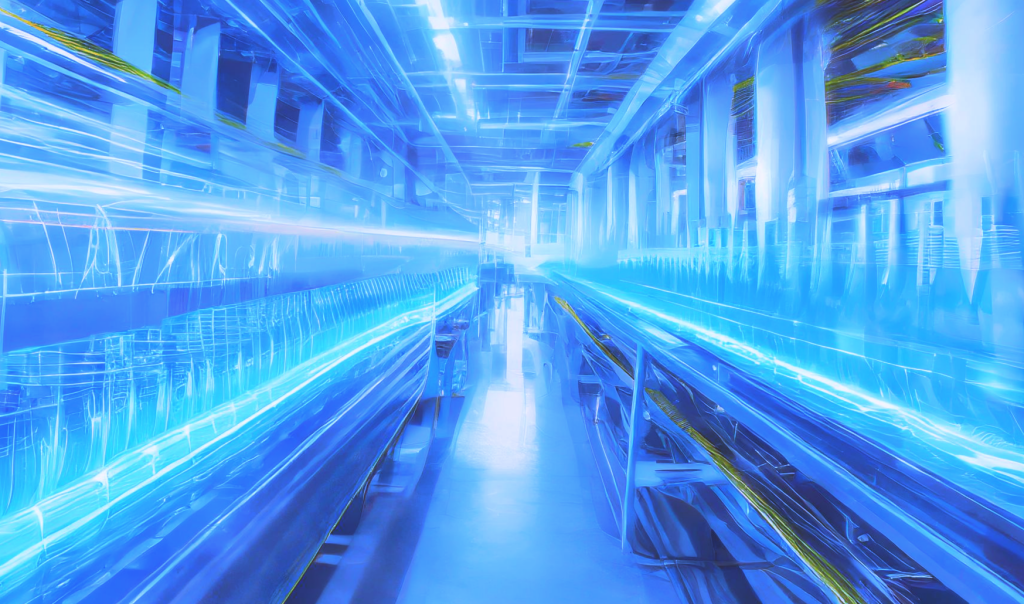
Key Drivers for Lean Continuous Improvement in Manufacturing
All manufacturing plants should embrace lean continuous improvement. Not matter the output volume, number of employees, or complexity of the operation, lean continuous improvement principles will undoubtedly eliminate waste.
Lean continuous improvement is a systemic, routine, and cyclic improvement process that will drill down pain-points in any manufacturing process.
With operators and floor managers tuned-in to actively identify waste, and take swift action on how to eliminate it, efficiency will increase, giving plants significant competitive advantage.
The key driver for your plant to develop lean manufacturing and a continuous improvement strategy is the fact that no plant is perfect, and almost all production processes can be improved.
The mindset of lean continuous improvement in manufacturing:
Is lean continuous improvement in manufacturing a strategy? No… it’s a mindset.
Lean continuous improvement is more than checkbox, it’s more than spreadsheets, or some scribbles on a whiteboard.
The Lean manufacturing approach and continuous improvement needs to be adopted across a plant. It’s a driving force to do better, and to make shifts more efficient, and ultimately more fulfilling for operators and plant managers.
Instead of working around issues on the plant floor, why not work to fix them? The practice of lean manufacturing continuous improvement allows for incremental improvement – that means that issues can be worked out over time.
Removing these pain-points and bumps along the manufacturing process certainly improves efficiency and eliminates wasteful work processes, but also eases frustrations and makes the workday smoother for shop floor employees.
Fully guided process
Audit data, methodology and line balancing software, all in one
Not just production line balancing software, our team provides a guaranteed manufacturing line balance step-change. We’ll guide you through a data-informed audit, implement five levels of control and train your team to use LineView’s line balancing software – all for long-term results.
Built-in benchmarking
Line balance scores make benchmarking easy
Making production line balancing easy is the key to lasting results. Easy-to-understand production line balance scores for every product type with built-in baseline comparisons are built-in within LineView’s line balancing software. Teams can benchmark live data vs. historical- so you’ll never lose your capacity gains.
Additional performance gains
Optional controls to automate restarts and recover speed
Optional manufacturing line balance control unlocks additional performance gains between 2-5%. This supervisory line control module sets optimal restart times on core machines (filler, labeler, packer) to accelerate recovery after downtime.
What is Lean?
Benefits of Lean
Lean manufacturing and the mindset of lean improves plant efficiency, reduces waste, and increases productivity.
Embracing lean manufacturing solutions across the shop floor will lead to increases in OEE, as each of the six losses will be systematically reduced.
As process improves and production is optimised, operators will be able to focus on their jobs, and not on the problems holding back output. On top of that, giving more responsibility and trust to operators and floor managers to identify issues will make their shifts more purposeful.
From a sustainability standpoint, lean manufacturing is the original way to be green. By eliminating waste through lean, your plant will be best suited to meet increasingly strict environmental and sustainability requirements.
Misconceptions about Lean
For a concept that’s been around for nearly 100 years, there are many myths and misconceptions about lean in manufacturing. For the manufacturing industry, the top three misconceptions are:
- Myth: Lean kills jobs. Fact: Lean only optimises jobs and makes processes run smoother, with less waste. Operators have more time to focus on their real work, to boost output and increase efficiency.
- Myth: Lean is expensive to implement. Fact: The lean mindset is free! Of course, training and some programmes are necessary. But adopting lean and training staff members throughout a business can be inexpensive with the right strategy. In the end, lean will save money through the elimination of waste.
- Myth: Lean requires complicated formulas, flowcharts, and processes. Fact: Lean is simple: incremental small change drives continuous improvement and elimination of waste. Often, methodologies like Six Sigma are paired with lean, and they do require a bit more involved strategy and analysis. But lean manufacturing and the lean mindset do not require complex techniques like Six Sigma.
Basics of Lean Manufacturing Continuous Improvement Processes
Across the manufacturing industry, general lean processes have been defined to establish metrics to evaluate lean’s impact.
We call those the Five Principles of Lean Continuous Improvement in Manufacturing.
What are the Five Principles of Lean Manufacturing?
1. Value
The determination of which features create value in a product is made from both internal and external customer standpoints. Value is expressed in terms of how the specific product or service meets the customers’ needs, at a specific time or at a specific price.
2. Value Stream
The entire sequence of activities across all parts of the organisation involved in delivering the product or service. This represents the end-to-end process that delivers value to the customer. These activities can be Value-Added or Non-Value Added.
Value Added Activities: An activity that transforms or shapes (for the first time) material or information to meet customer value.
Non-Value Added Activities: Activities that do not contribute value to the product or service (as seen by the customer). By clearly defining Value for a specific product or service from the end customer’s perspective, all non-value activities can be targeted for removal.
3. Flow
Flow is the uninterrupted movement of product or service through the system to the customer. Once non-value added activities (wastes) are identified and removed from the process, the product or service will flow through the value-added activities and to the customer.
4. Pull
Pull is about understanding the customer demand on your service and then creating your process to respond to this. A pull system will help you produce only what the customer wants when the customer wants it.
5. Perfection
Flow and pull are created and established, but do not stop there. Lean continuous improvement powers you to continuously look at making efforts to remove non-value added activities, improve flow and maximise customer satisfaction.
While continuous improvement in lean manufacturing focuses on removing waste, improving flow and continuous improvement, it also has other advantages. Quality is improved. The product spends less time in process, reducing the chances of damage or obsolescence. Simplification of processes results in reduction of variation. As the organisation looks at all the activities in the value stream (through value stream mapping), the system constraint is removed and performance is improved.
Lean manufacturing and continuous improvement involve many people in the value stream. Transitioning to flow thinking causes vast changes in how people perceive their roles in the organisation and their relationship to the product.
The organisation must be ready to accept and deal with change and understand different people will take on change at different paces.
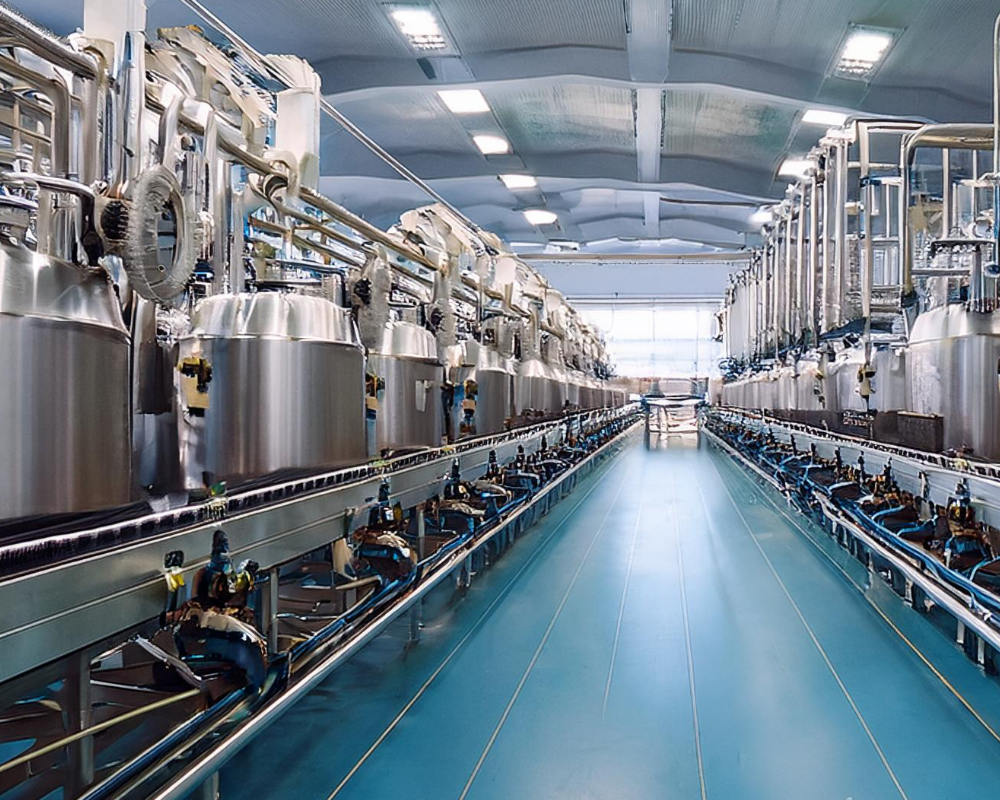
What is Continuous Improvement in Manufacturing?
Continuous Improvement Model in Manufacturing
Continuous Improvement (CI) Model is a framework to help identify, analyse, and optimise processes through continuous improvement initiatives. Continuous Improvement Model is an iterative process: there are four main principles of CI.
What are the 4 principles of CI?
Plan – Do – Check – Act
Plan: Establish objectives for specific or global process improvements based on the current state
Do: Perform necessary work to meet those objectives
Check: Perform tests on the method to validate and analyse the results on a continuous basis.
Act: Put into action the process improvement. Closely monitor results. If additional improvement to the process is possible, repeat the Plan-Do-Check-Act cycle to further eliminate waste, reduce inefficiencies, and improve operations.
Real-time and historic data from each process is invaluable throughout the CI Model to drill-down results and have a holistic view on the improvement initiative.
Manufacturing Continuous Improvement Methodologies
Along with the four principles of CI, there are certain helpful methodologies that can improve continuous improvement efforts on the shop floor.
Root Cause Analysis
When a problem occurs, it’s essential to understand why. When engaging in continuous improvement in manufacturing, getting to the root cause of any issue is the first step to fix a broken process.
There are several ways to perform a detailed root cause analysis. Digital solutions that plug directly into the shop floor can offer full visibility and give operators, floor managers, and senior leaders the best data to get to the root causes of every issue.
Lean Kanban
If you’ve worked in a lean company, Kanban might look familiar even if you’ve never heard the term. You may have seen large whiteboard with post-it notes (or Kanban boards), stickers, and arrows.
Essentially, Kanban is a lean workflow management method. It’s a way to visualise lean and continuous improvement projects through the use of easy to read and understand charts and diagrams.
Kanban is effective at helping teams see a direct and clear path to project workflow to help with process improvement.
Lean Six Sigma
Six Sigma is a set of statistical and data-driven techniques and tools within the context of lean that can help identify and minimise mistakes and defects.
It’s a detailed quality-control process that only allows 6 standard deviations (6σ) between average and acceptable limits for reducing manufacturing defects to no more than 3.4 occurrences per million units or events.
Six Sigma is a powerful scientific approach to be used within the lean framework but, as mentioned previously, involves specialisation and more complex analysis.
WIP Limits
WIP (Work in Progress) limits are constraints on how many items are actively being worked on at any given time. In terms of Continuous Improvement in manufacturing, this could mean how many processes each individual worker or team is actively trying to improve using the Manufacturing Continuous Improvement model.
WIP limits help to reduce risk, and keep CI initiatives under control, without overwhelming team members with too many ongoing projects.
How to maximise value with Lean Continuous Improvement
Embrace digitalisation with lean manufacturing and Continuous Improvement
At Lineview, we’re passionate about setting up plants to be future-proof and agile in an increasingly digital manufacturing landscape.
Integrating cutting edge technology and digitalisation does not mean the principles of lean continuous improvement in manufacturing can be ignored. The opposite is true.
As shop floors continue to become more digital, more autonomous, and more connected, lean continuous improvement mentality will enable shop floors to excel on their quest to eliminate waste.
Tackle your waste through embracing lean continuous manufacturing philosophy. Sign up for a free operational audit or Lineview Academy to let us help your operational teams harness the true power of lean.
Zero downtime and 10% OEE improvement are easier with causal loss.
Instead of focusing on individual downtime events, LineView helps you move beyond the symptoms to the true cause of downtime.
Improved OEE, downtime monitoring of microstops, auto fault analysis and productivity tools are the tools your team need for sustainable downtime reduction. And as a bonus? Get a guaranteed 10% efficiency improvement.
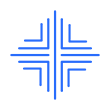
Be proactive to prevent machine downtime
Minimum 10% OEE gains
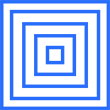
Go beyond symptoms to true causes of downtime
Faster changeovers
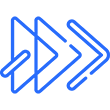
Get accurate unplanned equipment downtime statistics
Reduce (or eliminate) costly microstops
Customer stories
Dive into how Lineview empowers manufacturers to transform production. We believe success is a two-way street (win-win), so explore how our customers win big, and how their success fuels our drive to keep innovating.
Case Study
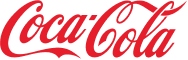
Coca-Cola Enterprises selects Lineviewâ„¢ as their system of choice.
Over a three-year period, LineViewâ„¢ has been implemented on every production line in Europe to help increase efficiency and reduce manufacturing costs.
Case Study

AB InBev China achieves Goals through Data, focus and action.
The world’s largest brewer, AB InBev, recommended LineView™ to their Chinese bottling plant based in Wuhan to remedy the company’s struggles with efficiencies.
Case Study
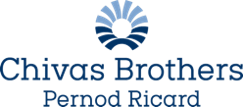
Chivas Brothers Pernod Ricard increases mechanical efficiency by 17% in six months.
Line 33’s Mechanical Efficiency increased from 60% to 70% after six months of data-driven interventions and focused improvements.