In today’s highly demanding manufacturing landscape, production line capacity is no longer just a number but often the lifeline of whether the business can answer the market’s demands—or not.
Thus, for modern manufacturing businesses, understanding and optimizing production line capacity is critical for unlocking growth and staying competitive.
Looking for ways to improve the capacity of your production line but don’t know where to start? You’ve come to the right place.
In this blog post, we will provide you with a comprehensive guide on how to improve your production line capacity, complete with actionable best practices and strategies you can implement right away.
We’ll cover:
- The concept of production line capacity and how it impacts manufacturing efficiency
- Identifying bottlenecks and inefficiencies in manufacturing
- Using lean manufacturing principles to improve production capacity
- Advanced technology integration
- Workforce training and skill development
- Scalable equipment and infrastructure
And more!
Without further ado, let us embark together on this journey to improve your production line capacity right away.
Understanding Production Line Capacity
Production line capacity refers to the maximum volume of products that a production line can produce within a given period of time. It is often measured in units per hour, shift, or day.
Production line capacity is a critical KPI for any production line or factory, defining the upper limit of the production line’s capabilities.
Calculating Production Line Capacity
To calculate production line capacity, we can use the following formula:
Production Line Capacity = (1 / Cycle Time) x Time Frame
Where:
- Cycle time refers to the time needed to complete one production cycle. A full production cycle must include all the steps required in the manufacturing process.
- Time frame is the period of time over which you want to measure production line capacity (i.e., 1 hour, 1 day, 1 shift, etc.)
For example, if a production line has a cycle time of 3 minutes (0.05 hours), and you want to calculate the production capacity in a 6-hour shift, you would use the formula as follows:
Production Line Capacity (per shift) = (1 / 0.05) x 6
Production Line Capacity (per shift) = 20 x 6
Production Line Capacity (per shift) = 120 units
So, with a cycle time of 3 minutes, the production line can produce 120 units of products in one shift.
The 6-Month Change Plan to Achieve 6-10% OEE Improvement
Drive Measurable Results Across Every Line.
- Eliminate production inefficiencies
- Turn problem lines into high-performing assets and reclaim your time
- Meet benchmarks in performance against global F&B leaders across OEE, sustainability, labor utilization
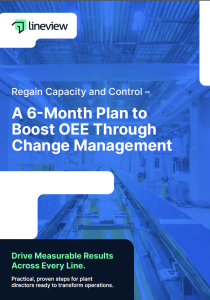
Production Line Capacity vs. Efficiency
Capacity has a close relation to efficiency—which is the ratio of output to input.
When a production line has a low capacity, it will naturally be less efficient than a production line with an excessive capacity. A production line with insufficient capacity will be more likely to experience bottlenecks, which will cause lower efficiency, delays, and even downtime.
Using the above example, where the production line has a capacity of 120 units/shift (or 20 units/hour), if this production line is producing 20 units per hour, it is operating at the most efficient state it can be in, its full capacity.
However, if the production line is only producing 15 units per hour, it is operating below full capacity. This means that the production line is not efficient and is wasting resources, which can be caused by a number of factors: machine breakdown, equipment failure, employee error/absenteeism, bottlenecks, and so on.
Production Line Capacity and Profitability
Besides its relationship with efficiency, which will affect profitability, a production line with insufficient production capacity will also not be able to meet its customer demand, which can lead to lost revenue and profits.
If a business has a capacity of only 120 units per hour, and yet it is receiving orders for 200 units per hour, it won’t be able to meet all of these orders, which can result in a disappointed customer, lost sales, and reduced profitability.
However, a business with excessive production capacity that can’t get enough orders will also be less profitable. The higher the production capacity, the more resources the business must invest in to maintain this capacity. An excess capacity means the business is paying for resources that are not used efficiently, lowering profitability.
The Importance and Benefits of Monitoring and Increasing Capacity
Why is it critical for businesses to monitor and improve their production line capacity? Here are some key reasons:
- Meeting market demands: As discussed above, a high capacity means the business is more ready to meet market demands. In today’s business landscape, customer demands may fluctuate rapidly. A high production line capacity provides the business with more flexibility to adapt to this rapidly and constantly changing market demand.
- Cost efficiency: Economies of scale dictate that it’s always more cost-effective to produce more units. By maximizing production line capacity, the business can reduce the cost per unit in its production process.
- Improved lead times: Faster production cycles and higher capacity will result in shorter lead times. This can be a great selling point in winning new clients and customers, especially those in industries where speed is an important factor.
- Revenue growth: Higher production line capacity typically means the ability of the business to take on more customers or meet larger orders. This will naturally result in increased market share and revenue.
- Reducing waste: Increasing production line capacity typically involves improving efficiency, streamlining manufacturing processes, and reducing waste in the process. This is not only important for the business’s bottom line but will also contribute to environmental sustainability.
Don’t wait – better line performance starts here!
Increasing Production Line Capacity: A Practical Guide
Effectively increasing production line capacity can provide various benefits for the manufacturing business, and in this section, we’ll have a closer look at how to practically increase this production line capacity.
Step 1: Assessing Current Production Capacity
The first and very important step in any initiative to increase production output and capacity is evaluating your current capacity.
By understanding where you currently stand, you can make informed decisions about how you should improve your process and eliminate bottlenecks.
There are various methods available for evaluating your current capacity, but here are the most common ones:
- Historical data analysis: This method involves reviewing and analyzing past production records like historical output, takt time, and machine efficiency to identify trends and patterns in the manufacturing process.
- Time and motion studies: Another common method that involves timing (recording) and observing the time and movement in each step in the production process. Useful for identifying bottlenecks and areas where efficiency can be improved.
- Workforce assessment: Evaluating the skill and productivity levels of the employees involved in the manufacturing process. The idea of this assessment is to weigh whether the workforce is operating at its full potential.
- Equipment utilization: Observing and evaluating the utilization of equipment and machinery, whether they are running at maximum efficiency or whether there are frequent downtime and failures.
- Simulation modeling: Creating a computer (AI-generated) model of the production line to simulate different real-life scenarios. This method can be effective for identifying inefficiencies, bottlenecks, and problems that may occur during the production process.
- Benchmarking: Comparing the production line’s performance to other lines or other processes.
The 6-Month Change Plan to Achieve 6-10% OEE Improvement
Drive Measurable Results Across Every Line.
- Eliminate production inefficiencies
- Turn problem lines into high-performing assets and reclaim your time
- Meet benchmarks in performance against global F&B leaders across OEE, sustainability, labor utilization
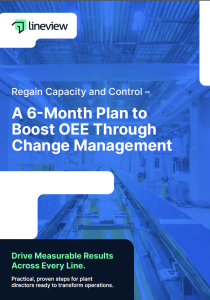
Important metrics to measure
Regardless of the method you use, the goal of the evaluation/assessment process is to collect data and metrics relevant to identifying bottlenecks and areas for improvement.
Some of the important metrics to be collected and analyzed including:
- Production output: The number of units/products produced by the production line in a given timeframe. Also called “throughput.”
- Machine efficiency: The percentage of time that a machine is producing units/products in an optimal performance.
- Takt time: The amount of time available to produce one unit or product. Calculated by dividing the available production time by customer demand. For example, if the production line operates for 6 hours per day and the customer demand is 60 units per day, then the takt time is 6 minutes.
- Overall Equipment Effectiveness: Or OEE, is a comprehensive metric that takes the availability, quality, and performance of a piece of equipment. OEE offers insights into the equipment’s efficiency and its impact on production capacity.
- Downtime: The amount of time when a machine or the entire production is not operating, for example, due to maintenance, changeovers, or breakdowns. The lower the downtime, the higher the capacity.
- Product quality: The percentage of produced products that meet the client’s requirements or the required quality standards.
Step 2: Identifying Bottlenecks and Constraints
Bottlenecks refer to areas in the production process where there is a limited output or a delay. Identifying and keeping track of bottlenecks is critical for optimizing production line capacity.
Bottlenecks can occur anywhere in the production line from start to finish, preventing the line from operating at its full capacity, and can be caused by a number of factors, including:
- Machine failure/breakdowns: When a machine fails to operate, it can stop or delay the entire production line.
- Operator errors: An insufficient number of operators, unskilled laborers, or mistakes by operators can slow down or stop production.
- Non-optimal production line layout: A poorly designed production line, especially if there are a lot of movements of raw materials and/or operators, can lead to bottlenecks.
- Unbalanced production line: When some operations in the production line are more time-consuming than others, it can lead to delayed operations.
- Lack of inventory: An insufficient number of raw materials or inventory of finished goods can hinder the operation flow.
- Space: Lack of space for operator movement, storage, or additional equipment can cause bottlenecks.
Don’t wait – better line performance starts here!
How bottlenecks impact efficiency and capacity
When a bottleneck occurs, it can lead to various negative impacts on production efficiency and capacity that can’t be overstated:
- Reduced throughput: Bottlenecks can lead to a reduction in the production line’s overall output since the production line is only able to produce as many units as the bottleneck task/operation. This can ultimately lead to unmet customer demands.
- Increased waste: WIP (work-in-progress) inventory can accumulate before a bottleneck, and the production line may need to keep more inventory on hand to buffer against the delays and downtime caused by the bottleneck. This will lead to increased inventory costs.
- Unpredictability: Delays introduced by bottlenecks can make production timelines more unpredictable. This may disrupt your production plan and schedule, frustrating your team and customers.
- Lower profitability: Higher costs and missed sales opportunities caused by bottlenecks will ultimately cause lower profitability.
- Overworked labor and equipment: Workers and the machinery at bottlenecks may experience stress and overuse. For workers, this may result in burnout and reduced productivity, while for machines, it can lead to increased needs of maintenance and delays.
How to identify bottlenecks
There are a number of ways to identify bottlenecks and constraints, and some of the most common methods are:
- Observation: Careful observation of each operation in the production line to identify areas where equipment frequently slows down (or stops entirely) and areas where work accumulates.
- Data analysis: Reviewing and analyzing historical data on throughput, cycle times, and overall process performance to identify abnormal patterns or operations with consistently longer times.
- Process mapping: Creating a visual map of the production line’s process with the help of software tools. Having a comprehensive visual diagram can help us identify operation stages with frequent delays and excessive wait times.
- Employee feedback: Collecting feedback from laborers involved in the production process can be valuable, as they may have valuable insights into where bottlenecks, delays, and constraints exist.
- Simulation tools: Simulation software can allow you to accurately model your production line. These models can help you identify bottlenecks early because they cause actual problems in the production process.
Step 3: Develop a Strategic Plan
Now that we’ve assessed the current state of our production capacity and identified the bottlenecks, we can move on to developing a strategic plan to improve the production line capacity.
The first thing you should do is to define the objectives of your capacity improvement initiatives.
Identify goals and objectives
It’s critical to set clear and specific objectives before planning your strategic initiatives. Some examples you can consider:
- Increasing production output by a certain percentage in a specific timeframe
- Reducing lead times
- Improve product quality without compromising capacity
- Reduce production costs
- Meeting a higher customer demand
And so on. Define your goals as clearly and as specific as possible, so you can get a clear direction for your strategic plan.
The 6-Month Change Plan to Achieve 6-10% OEE Improvement
Drive Measurable Results Across Every Line.
- Eliminate production inefficiencies
- Turn problem lines into high-performing assets and reclaim your time
- Meet benchmarks in performance against global F&B leaders across OEE, sustainability, labor utilization
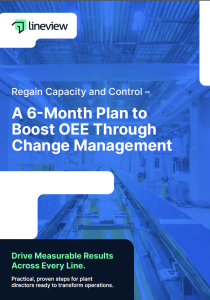
Choosing strategies to boost capacity
Based on your assessment of the current production capacity and the goals you’ve defined, you can start planning your strategies.
There are various effective strategies you can consider when it comes to increasing production capacity, each addressing different aspects of the production process. Here are some of the most effective ones you can consider:
- Process optimization
This strategy involves identifying bottlenecks in the production process so we can eliminate these bottlenecks to reduce waste, reduce cycle times, and enhance production efficiency.
We can streamline the production process by using lean manufacturing principles, such as Kaizen (continuous improvement), Six Sigma, and just–in–time (JIT) inventory, among others.
Pros of process optimization:
- Reduced waste production
- Cost-effective
- Improved product quality
- Increased capacity
Cons of process optimization:
- Identifying bottlenecks and implementing improvements can be complex and time-consuming
- Employees and operators may show resistance to change
- Equipment upgrades
Another effective option is to invest in newer or more advanced machines/equipment or upgrade your existing technology that is faster, more reliable, and/or more efficient.
For example, you can consider investing in new machines that have a higher innate capacity, so they can produce more units per hour. Automated equipment and visual factory tools can also help streamline your processes, freeing your workforce’s time so they can work on other tasks that can contribute to increasing production line capacity.
Pros of equipment upgrades:
- Quick and easy to implement
- It can be very effective in improving speed, accuracy, and reliability
- Can reduce labor costs
Cons of equipment upgrades:
- High upfront investment costs
- Potential downtime when installing new equipment/machines
- Need to train operators on using new equipment
- Labor management
This approach involves optimizing your workforce productivity. For example, through more efficient scheduling, training/skill development, optimized resource allocation, etc. Cross-training operators to help them acquire new skills, hiring more skilled/experienced laborers, and implementing new work management practices can also help boost production capacity.
Pros of labor management:
- Cost-effective
- Successful improvement of employee morale can be sustainable
- Better improved agility and flexibility than other methods
Cons of labor management:
- Labor management changes, training, and adaptation can be time-consuming
- Finding and retaining qualified talents can be challenging
- Layout redesign
If the existing production line’s layout is not yet optimal, reconfiguring the layout may help improve the flow of operators, minimize material handling, reduce bottlenecks due to material/operator flow, and improve production capacity.
Don’t wait – better line performance starts here!
Pros of layout redesign:
- Relatively easy to implement
- Can also improve workplace safety
- Effective in optimizing existing resources by reducing consumption
Cons of layout redesign:
- Can disrupt production and cause downtime
- Upfront investment costs can be high due to physical changes
- Technology integration
This strategy involves incorporating new technologies into the production line, like automation, robotics, and data-driven optimization and production line balancing tools to improve production efficiency, precision, production speed, and consistency.
A business might invest in automated robots to execute repetitive tasks or in smart factory software like LineView to better track and manage production data. For example, in the food industry, investing in automated packaging machines can significantly improve packaging speed and precision, which will contribute to increasing capacity.
Pros of technology integration:
- Automation can be very effective in improving production speed, precision, and consistency
- Can reduce labor costs
Cons of technology integration:
- High upfront investment costs
- The need for skilled technicians to operate the new technologies and may need additional training costs
- Potential system failures
Step 4: Implementing Changes
Once you have developed a strategic plan to improve production line capacity, this step is about implementing that plan.
Here are the critical steps involved in implementing the changes:
- Communicate the plan to your team. It’s important to communicate the plan to your employees and stakeholders as early as possible and collect their feedback. This can be very important in ensuring your team is on board with the changes and that your team members properly understand their roles in the initiatives.
- Develop a detailed implementation timeline. This timeline/plan should include the specific tasks, the timeline for each task, and the resources needed to complete them. A well-defined timeline can help ensure the plan is implemented smoothly and minimize potential disruption.
- Training and skill development. If your plan involves investing in new equipment and technologies, it’s important to train your team on how to use them. It’s critical that your team is able to operate the new technologies effectively and efficiently to ensure a smooth implementation of the plan.
The 6-Month Change Plan to Achieve 6-10% OEE Improvement
Drive Measurable Results Across Every Line.
- Eliminate production inefficiencies
- Turn problem lines into high-performing assets and reclaim your time
- Meet benchmarks in performance against global F&B leaders across OEE, sustainability, labor utilization
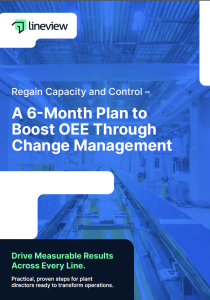
Step 5: Monitoring and Continuous Improvement
Once the changes have been successfully implemented, it’s still important to monitor the production line’s performance on an ongoing basis for a few reasons:
- It ensures you have the ability to meet customer demand
- Identify bottlenecks and potential problems as early as possible, so you can fix the issues ASAP
- Keep track of the progress of any changes you’ve implemented to improve production line capacity
Here are some tips on how to properly monitor your production line’s performance and ensure continuous improvement:
- Select relevant KPIs: Start by choosing the right KPIs to monitor how your capacity-increasing initiatives are performing. These may include production throughput, OEE, downtime, cycle time, and reject rates.
- Establish benchmarks: Establish benchmarks based on the initial production capacity you’ve identified in the initial assessment. This baseline data will serve as your reference point in measuring progress.
- Regular and reliable data collection: Establish a system that can help you implement consistent data collection and reporting. Timely and accurate data collection is very important.
- Identify and analyze trends: Identify trends and patterns so you can uncover areas where your production capacity is still lacking or exceeding your expectations.
- Visualize data: Leverage charts, graphs, and other data visualization methods to help you interpret complex and large volumes of data. Visualization can also help you identify trends and anomalies.
- Review and improve: Regularly review the KPIs to assess your production line capacity. Adjust your strategy accordingly when your KPIs are not meeting your goals.
Conclusion
Increasing production capacity can help your business reduce production costs, consistently meet customer demand, and improve customer satisfaction.
In this article, we have covered the practical ways on how you can improve production capacity, from how to identify bottlenecks to the effective strategies that boost production capacity to how to ensure continuous improvement.
By using what we’ve learned in this article, you are ready to transform your production line into a highly efficient system capable of meeting customer demands with excellence and efficiency. All it takes is your commitment to take action.