OEE (Overall Equipment Effectiveness) is one of the most important performance metrics to monitor for manufacturing businesses. Knowing your baseline OEE can help you measure and evaluate your business’s productivity, while improving OEE will have a direct impact on improving the business’s performance and overall profitability.
In this guide, we will discuss how to improve your OEE and measure your business’s true OEE potential, but let us begin from the basics:
What is Overall Equipment Effectiveness (OEE)
Overall Equipment Effectiveness, or OEE, is a term coined by the late Seiichi Nakajima—the pioneering founder of the TPM (Total Productive Maintenance) system—back in 1960.
Basically, OEE is a calculation method for measuring how effective a machine or equipment is in achieving its desired objective. For example, if a piece of equipment is designed for manufacturing 1,000 iPhones in an hour, then it will have an OEE score of 100% if it can manufacture 1,000 of only good iPhones in an hour.
An OEE score of 100% means the equipment has achieved:
- 100% in Quality (only producing good parts without any defective parts)
- 100% in Performance (as fast as possible without any delay)
- 100% in Availability the equipment is always running during the query time
With that being said, OEE can be calculated with the following formula:
OEE (%) = Availability (%) x Performance efficiency (%) x Rate of Quality Product (%)
Further below, we will discuss how each metric (availability, performance, quality) is calculated.
The importance and benefit of OEE
OEE is mainly used as a performance indicator to assess the availability, performance, and production quality of a machine or a system and is the most beneficial when used in a manufacturing company.
OEE can be beneficial in the different levels of a manufacturing company’s environment, including but not limited to:
- Providing a reference point for the company when planning its operations by offering a clear picture of how the company’s system currently performs
- Allowing the company to identify ineffectiveness, bottlenecks, and inefficiencies in its tools, machines, or systems. By enabling the company to pinpoint any problem accurately, problems can be fixed faster and better.
- Allowing the company to pinpoint any ineffective machine or tool, so the company may decide to fix or decommission it.
- Providing a clearer picture of potential loss due to production issues.
- Understanding the impact of Planned downtime such as Changeovers, Breaks, Maintenance, etc
The 6-Month Change Plan to Achieve 6-10% OEE Improvement
Drive Measurable Results Across Every Line.
- Eliminate production inefficiencies
- Turn problem lines into high-performing assets and reclaim your time
- Meet benchmarks in performance against global F&B leaders across OEE, sustainability, labor utilization
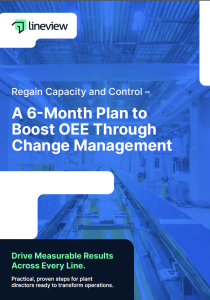
Three Core Elements of Overall Equipment Effectiveness
Above, we have briefly discussed how there are three core elements of OEE: availability, performance, and quality.
Understanding these different elements and how they affect the overall effectiveness of the equipment will also help in improving the OEE of the respective equipment.
Let’s discuss each of these elements in a more in-depth manner:
- Availability
Availability refers to the ratio between the actual run time of a machine and the desired production time within the available time frame.
Availability score can be calculated with the following formula:
Availability = Actual Run Time / Desired Production Time
For example, if the planned production time of a specific piece of equipment is 70 hours a week, while the actual run time of this equipment is only 50 hours at any given week, then the availability score is 50/70=71.42%
A low Availability score is typically caused by poor maintenance, causing frequent downtime. This downtime can happen when there’s any failure/problem with the equipment, when the machine requires any maintenance/parts replacement/fuel filling, when there are frequent or ineffective changeovers or when the machine needs to be adjusted/configured in one way or another.
- Performance
Performance efficiency refers to whether the manufacturing process of the equipment can run at the maximum possible speed when it is running, which is the ratio between Net Run Time (the fastest possible time to finish the manufacturing process) and the Actual Run Time.
Performance efficiency can be calculated with the following formula:
Performance = Net Run Time/ Run Time
While Net Run Time can be calculated as Ideal Cycle Time × Total Count, with Ideal Cycle Time being the fastest possible time, the equipment can produce one part.
Meaning, we can also use the following formula:
Performance = (Ideal Cycle Time × Total Count)/ Run Time
For example, a machine has the theoretical capability to manufacture 400 pieces of products per shift (1 shift is 8 hours or 480 minutes), while in the past shift, it has produced 360 products (including defects) on average.
With this example, the machine has an Ideal Cycle Time of 0.833/minute, a Total Count of 360, and a Run Time of 480 minutes. The Performance Score is (0.833 x 360)/480=0.625 or 62.5%, which is a pretty low score.
- Quality
The rate of quality, as the name suggests, is the ratio between good (non-defective) products and the total number of products manufactured.
The formula for calculating quality is quite simple:
Quality=Good Count/Total Count
For example, in a manufacturing process, a machine manufactured 300 pieces of parts per shift, and 20 of these are defective.
Using the above formula, then:
Quality= (300-20)/300= 0.933 or 93.3%
Actionable Strategies to Improve OEE
Now that we’ve understood the three core components of OEE, we can get a clearer idea of how improving a machine’s (or the whole company’s) OEE is about improving one or more of these components.
For example, if a machine has 90%+ scores in quality and performance, but doesn’t score too well on availability, then it’s quite obvious that we should improve its availability score to improve the overall OEE.
Don’t wait – better line performance starts here!
Understanding this basic principle, here are some actionable tips and strategies you can adopt to improve your Overall Equipment Effectiveness.
- Set realistic OEE goals and objectives
You won’t be able to improve your OEE if you don’t know what to improve.
It’s crucial to first understand what the bottlenecks and challenges are in your equipment, so you can define the right objectives.
First, assess and calculate the OEE potential of each piece of equipment with the formulas we’ve shared above while considering equipment design, condition (i.e., how long it has been in operation), and current performance.
We’d recommend following the SMART goals principle when defining your objectives:
- Specific: rather than focusing on too many things at once or having goals that are too general, it’s best to set objectives that are as narrow-focused as possible.
- Measurable: you should be able to measure your effort’s performance against this objective
- Attainable: or realistic. If you set goals that are too far-fetched, it can be counterproductive to your overall efforts.
- Relevant: is the objective relevant to your business’s end goal of being more productive and profitable?
- Time-bound: you should be able to clearly define the timeline to achieve this objective
Attainability is especially important when defining your OEE objectives. The average standard of what’s considered ‘good’ OEE is an 85% score. However, if your equipment currently has a 55% performance score, straight-up aiming for an 85% OEE score might not be realistic, and it’s typically better to set more incremental milestones.
Not to mention, not every piece of equipment can realistically achieve this gold standard of 85% OEE, so it’s important to first assess the improvement potential for each piece of equipment and benchmark your performance score against other manufacturing sites (inside and outside your organization).
- Display real-time OEE scores to your employees and stakeholders
Making OEE scores and other types of production/performance data available to your employees can benefit your company’s effort to improve OEE in several different ways:
- It promotes accountability. If, for example, a tool’s availability score gets lowered because of an error of a specific employee, the same issue can be avoided in the future.
- If any problem that affects OEE does occur, the availability of information allows your employees and stakeholders to be aware of it in real-time
- Allows team members to act quickly so they may be able to make adjustments that will change the end OEE score before it’s too late.
To maximize these benefits, how you display this data is also important, and we’d recommend visualizing this data in an engaging, presentable form (i.e., with charts, infographics, etc.)
The more real-time and visually pleasing you can display your data, the more engagement and commitment you’ll get from your employees, leaders, and managers. On the other hand, the more engaged your team is, the more likely you can achieve improvement in OEE.
The 6-Month Change Plan to Achieve 6-10% OEE Improvement
Drive Measurable Results Across Every Line.
- Eliminate production inefficiencies
- Turn problem lines into high-performing assets and reclaim your time
- Meet benchmarks in performance against global F&B leaders across OEE, sustainability, labor utilization
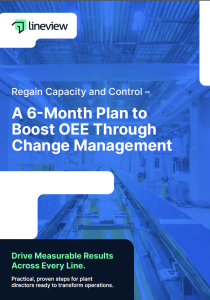
Automate data collection and reporting
To make real-time data reporting possible, the best practice is to automate the collection and reporting of OEE data.
Manual data collection and reporting is not only slow, but in practice, it’s also very challenging to perform. On the other hand, insufficient data is one of the biggest obstacles to improving OEE and productivity in general.
Fortunately, automating production data collection is now much easier and more affordable, thanks to various advancements in technology. LineView, for example, can perform automated OEE and True Causal Loss analysis on each of your production lines in real-time in an affordable manner.
There’s simply no reason to stick with manual data collection and rely on Excel spreadsheets with these better options. Automate your data collection, and focus your efforts on actually improving productivity and OEE.
- Identify your system’s Six Big Losses
When discussing OEE, the ‘Six Big Losses’ refers to the six biggest factors (two for each OEE core component) that negatively affect OEE scores, and they are:
Quality losses:
- Production rejects. Defective parts or products generated during the production process must be disposed of or reworked.
- Startup rejects. Any defective products/parts produced between the startup period and until the stable production state is reached. Can happen due to equipment that naturally requires a ‘warm-up’ period, but also sub-optimal changeovers or startups.
Performance losses:
- Small stops. Sudden shutdowns of equipment for a period lower than 10 minutes. may occur multiple times every shift and can add up.
- Slow cycles. When equipment runs at a slower speed compared to its theoretical optimal speed. Slow cycles typically happen due to poor maintenance.
Availability losses:
- Unplanned stops. When equipment is not working due to problems, failures, or sudden need for maintenance/repair that occur within the time otherwise scheduled for production.
- Planned stops. Scheduled/planned downtime for maintenance, cleaning, changeovers, etc. May be planned poorly, which will result in losses of potential availability.
When striving to improve OEE, it’s best to focus your attention on identifying and fixing any of these six losses in your equipment or system.
We can do this by conducting a thorough root cause analysis to identify the cause of each loss. It’s crucial to solve the actual root cause of each problem rather than spending your resources to treat symptoms repeatedly.
For each symptom of the six losses identified, perform root cause analysis (RCA) by following these steps:
- Define the symptom or the exact event
- Identify possible causes
- Narrow down and identify the exact root cause
- List down possible solutions and prioritize
- Take action
- Evaluate and verify solution effectiveness
These six losses can have a ripple effect on your equipment’s overall productivity, and by fixing them alone, you can dramatically improve OEE.
- Prioritise mission-critical equipment or system
While ideally, we should strive to improve the OEE of all tools, machines, and pieces of equipment, limited time and resources may prevent us from doing so.
Thus, it’s important to know how to prioritize and focus on improving the most important assets for your manufacturing process or business in general.
How should we prioritise? In general, we can choose between two main approaches:
- Strategic: choosing the assets that, when improved to be more efficient, will provide the most contribution to the business’s overall efficiency
- Reactive: choosing assets that show obvious bottlenecks or inefficiencies, especially those that have a negative ripple effect when they fail to function at their optimal levels
By prioritizing your assets properly, you can also have an easier time extending the OEE improvement efforts to other machines connected to the critical asset.
Remember that how you should prioritize your assets and direct your OEE efforts are unique to your business. What is valuable to your business may not be very valuable to others, so it’s important to really understand what’s critical to your business when prioritizing your assets and defining your OEE improvement strategy.
Don’t wait – better line performance starts here!
- Carefully plan your maintenance program
As we have discussed above, whether or not the asset received proper maintenance can significantly affect its Overall Equipment Effectiveness.
Ensuring your assets can stay running as much as possible is the key to availability, one of the three components of OEE.
So, having a proper maintenance program is very important if you really want to improve OEE.
When it comes to planning maintenance, there are two crucial challenges to consider:
- Cost: maintenance efforts can be expensive, both in terms of actual spending and potential revenue losses due to downtime caused by the maintenance efforts.
- Time: while maintenance may cause some downtime, it can prevent future issues and breakdowns that can potentially cause longer downtime. Smart and informed judgement on whether preventative maintenance measures are necessary is critical.
It’s recommended to implement machine downtime tracking software or adopt a predictive maintenance strategy so businesses can identify potential asset failures and treat the problem before it occurs to minimise downtime. On the other hand, businesses should find the right balance to avoid over-maintaining the equipment so the overall costs do not outweigh the benefits.
- Integrate assets to optimize workflow
While typically, the primary focus of OEE improvement is improving individual assets, connecting assets to ensure optimal information flow and minimise conflicting operations will also help in improving OEE.
The most important consideration when integrating different assets and systems is to make sure the data of machines and operators closest to production (the shop floor) is properly optimised for information flow.
We can use OEE Software by LineView to automate data collection from shop floor machines to ensure other management systems, such as ERP and CMMS, can receive accurate production data in real-time.
- Effectively address equipment failure via reason codes
For most manufacturing processes, Unplanned Stop is typically the largest source of ineffective production time.
Thus, addressing Unplanned Stops due to equipment failure is an essential aspect of OEE improvement.
Again, the key to fixing equipment failure is to identify and understand the root cause, and the best practice is to make use of reason codes. With reason codes, every cause of unplanned stops is given a specific code, so your team can easily understand this cause and quickly take the appropriate action.
Here are some tips on how to use reason codes effectively:
- Use as few reasons as possible, and not more than 25 reasons in total
- To keep as reason count low, create a catch-all reason like “other reasons” or “other losses” for reasons that can be treated with (relatively) generic solutions
- This catch-all reason (i.e., “other reasons”) should not be in your top ten reasons. Add reasons as needed for this purpose
- For reasons that you specify, make sure they are clear and specific so you won’t confuse them with other reasons
- Every reason should describe symptoms and not identify root causes
- Evaluate your reason codes usage, and remove reasons that aren’t used frequently, again to keep reason count low
- Minimize setup losses by establishing policies
Setup (also called changeover or make-ready) is another major source of losses in many manufacturing processes.
To prevent loss of production time, it’s important to establish consistent policies for setup and adjustment, especially in how you measure Setup Time.
There are two basic ways to measure Setup Time:
- Measured as the time between the last good part/product produced before Setup to the first good part/product produced after Setup.
- Measured as the time between the last good part/product produced before setup to the first state when the process consistently produces parts/products that meet quality standards after setup. In this definition, warmup or startup time is considered a part of the Setup time.
Another effective way to minimize Setup loss is to establish a Single-Minute Exchange of Die, or SMED.
SMED is, simply put, a collection of techniques for reducing the time needed to complete a Setup period to less than 10 minutes (single-digit.)
The basic idea of SMED is to breakdown the Setup into its smallest elements and assess whether each of these elements can be:
- Moved before or after the Setup (separated)
- Modified, so it’s no longer included in the Setup (converted)
- Made to be faster (streamlined)
For example:
- Preparing parts and tools needed for Setup in advance (Separating this process from the actual Setup)
- Use templates or marked settings to eliminate adjustments and configurations in every Setup (Converted)
- Put together all supplies necessary to complete the Setup in an accessible place (Streamlined)
The 6-Month Change Plan to Achieve 6-10% OEE Improvement
Drive Measurable Results Across Every Line.
- Eliminate production inefficiencies
- Turn problem lines into high-performing assets and reclaim your time
- Meet benchmarks in performance against global F&B leaders across OEE, sustainability, labor utilization
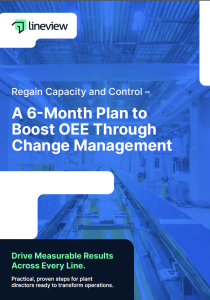
9. Minimise performance losses by identifying patterns
Evaluate your manufacturing process and try to identify patterns of frequent and/or significant performance losses, like an unusual number of small stops.
You should especially evaluate your process/system to assess the possibility of performance losses when there’s an environmental or part/material change. Also, check whether there are recurring losses during a specific shift.
Once you’ve identified a pattern, apply Root Cause Analysis (RCA) as discussed above to identify potential root causes and solutions.
Some potential solutions include:
- Schedule a preventative maintenance program
- Train operators on optimal and standardized work procedures to minimize human errors
- Set clear standards and policies to maintain material quality
- Improve the precision of the equipment
Wrapping Up
Ultimately, improving OEE is about identifying issues related to Availability, Performance, or Quality aspects of the manufacturing processes and finding potential solutions to fix these problems.
It’s also important to create a culture for continuous productivity improvements by establishing a simplified method for motivating your team members, such as providing real-time feedback regarding shift efficiency.