Value Engineering
Measurable ROI and Better Manufacturing Improvement Project Outcomes.
Manufacturing projects without the foundation of Value Engineering can lead to costly inefficiencies and missed opportunities. Lineview’s structured approach ensures your objectives are met with precision, optimizing resources for peak performance – all within your timeframe.
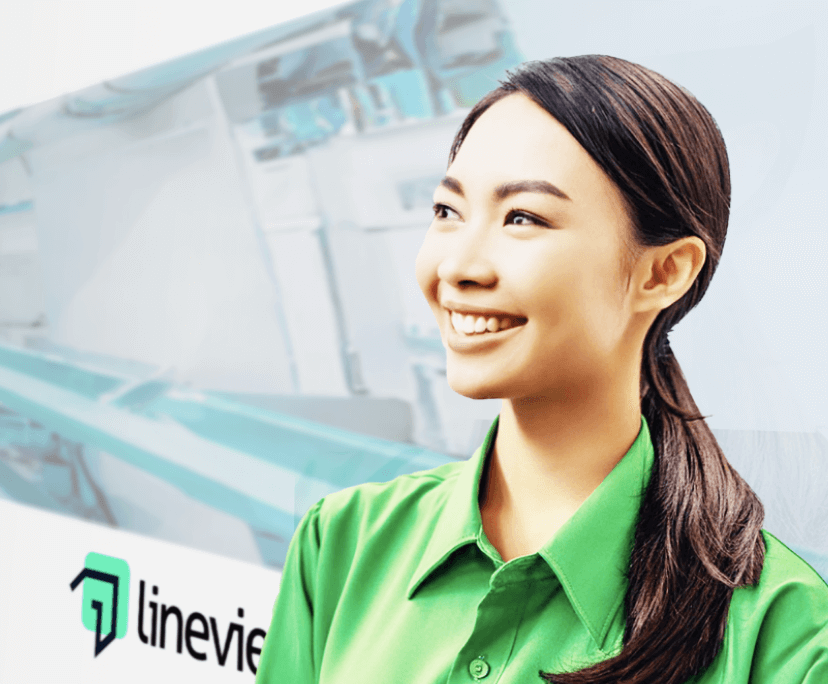
Value Engineering focuses on quantifying opportunities for a clear path to maximized ROI
LineView’s Value Engineering is characterized by its rigorous, ROI-focused process that ensures optimal performance across your manufacturing operations.
Phase 1 – Value Discovery
Initiate transformation with a Value Discovery Audit.
The Value Discovery Audit is a comprehensive analysis of your manufacturing processes, identifying the best areas for improvement and anticipated growth and/or cost savings.
The Value Discovery Audit is a comprehensive analysis of your manufacturing processes, identifying the best areas for improvement and anticipated growth and/or cost savings.
Read more
In-depth analysis: Uncovers operational inefficiencies and areas ready for improvement. Benchmarking: Evaluates against industry best practices to pinpoint where strategic enhancements can yield significant value. ROI opportunity plan: Crafting a value proposition with solid ROI projections to guide operational advancements.
Phase 2: Value Realization
Value Realization translates strategy into success.
Our Value Realization phase ensures the strategic insights from your audit are executed effectively, transforming analysis into real-world operational improvements and ROI.
Working side-by-side with our Customer Success team, we translate your project plan into tangible successes that are tracked with rigorous metrics. Our commitment to you is always turning analysis into measurable outcomes.
Phase 3 – Value Optimization
Lineview’s Value Optimization is a proactive approach to refining your operations.
LineView’s Value Optimization is a proactive approach to refining your operations. We put strategies in place that to sustain your wins and enhance performance gains over the long term.
You’ll also have our commitment to continuous process refinement. What does this mean? We work with your team to stay at the leading edge and tackle increasingly strategic opportunities.
Get the strategic advantage with Lineview’s Value Engineering.
We focus on optimizing your current processes for enhanced operational efficiency and sustainable cost savings, ensuring continuous improvement and long-term success.
Maximize Project Impact with Value Engineering
Tackling an enterprise-wide manufacturing improvement project relies on measurable ROI and achieving outcomes. Lineview’s Values Engineering team helps you reach those goals.
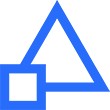
Measure and understand the opportunity before your project begins
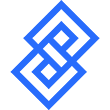
Transform complex data into clear, actionable strategies with ROI
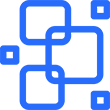
Drive continuous operational improvement and planned outcomes
Customer stories
Case Study
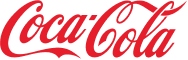
Coca-Cola Enterprises selects Lineview™ as their system of choice.
Over a three-year period, LineView™ has been implemented on every production line in Europe to help increase efficiency and reduce manufacturing costs.
Case Study

AB InBev China achieves Goals through Data, focus and action.
The world’s largest brewer, AB InBev, recommended LineView™ to their Chinese bottling plant based in Wuhan to remedy the company’s struggles with efficiencies.
Case Study
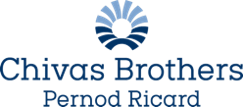
Chivas Brothers Pernod Ricard increases mechanical efficiency by 17% in six months.
Line 33’s Mechanical Efficiency increased from 60% to 70% after six months of data-driven interventions and focused improvements.