Reduce the cost of manufacturing with better insights to go beyond overall equipment effectiveness and realise your Factory of the Future.
The ultimate goal of the Factory of the Future is to reduce the cost of transforming raw materials to a saleable product. A lower cost of manufacturing creates new potential to re-invest and maximise operational efficiencies.
In these factories, OEE will still be a key metric on the shop floor as its usefulness and insight have long been proven to be extremely effective. Harnessing technologies including AI and Big Data; however, will allow manufacturers to go beyond OEE Systems and complementary manufacturing software as they evolve into a comprehensive platform providing manufacturing insights, and eventually AI-driven task management.
Maximising OEE Reduces Manufacturing Costs
Major costs in manufacturing are: assets which depreciate over time, labour to run the facility, maintenance and upkeep, utilities, overhead and cost of goods. When you move to the future, working with traditional OEE metrics will continue to help optimise these costs while working in tandem with other, even more intelligent and digital processes.
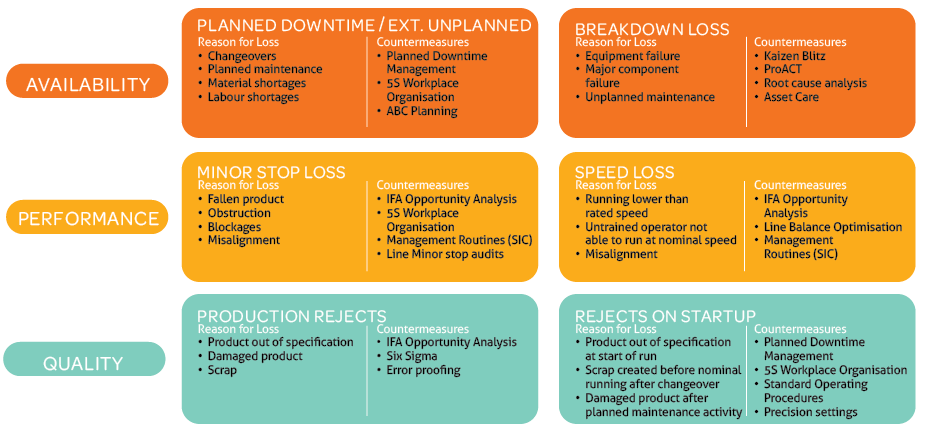
The Evolution of OEE Systems that Drive Manufacturing Insight
OEE is centred around minimising losses. Identifying and limiting planned downtime or external unplanned events, reducing speed loss, avoiding breakdowns and minor stops, and minimising both production rejects and rejects on start-up are all part of the major OEE evaluation criteria.
Hereโs how the successful execution of an OEE improvement strategy directly results in real-world cost savings and capacity gains.
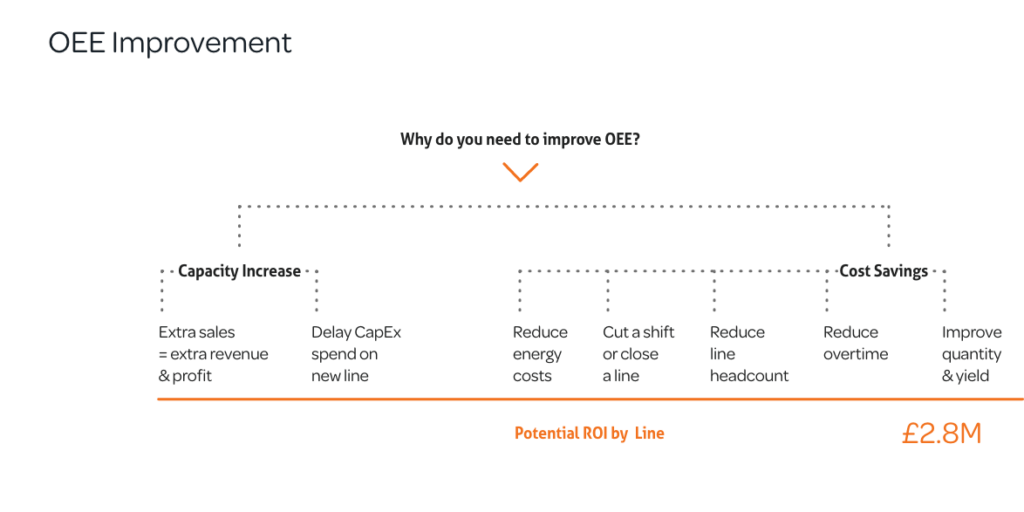
Improving OEE reduces costs, time and energy. Reduce energy cost, cut a shift or close a line, reduce line headcount and overtime, and improve quality and yield. Furthermore, maximising OEE can help drive capacity increase which generates extra sales and can allow for delays in CAPEX spend.
BEYOND THE SIX LOSSES OF OEE
Maximising labour through smart automation | Get manufacturing insight, not just KPI |
With OEE thinking, labour is maximised through more efficient processes and training to address areas of Availability, Performance and Quality loss.Labour should contribute to areas where automation is not possible. Automation can be optimised intelligently to help make an operatorโs tasks more seamless and empowering. For example, a machine can be fed material with drones and robots and the human operator is better able to solve problems and do tasks that cannot be automated. | End-to-end connected shop-floor monitoring and analysis systems offer major steps towards a smart, digital evolution. It serves as an essential step to first understand all plant processes โ such as waste, energy use and output โ then adapt and make changes as needed.Waste can be eliminated using smart manufacturing insights enabled through data management. For instance, Total Productive Maintenance (TPM) processes can be tracked and optimised, with every investment in maintenance and engineering monitored and evaluated using real-time and historical analysis. |
On-Demand Webinar
Factory of the Future: A Connected Ecosystem
Optimised at every stage of production, your smart connected factory is agile, transparent, efficient and future proof.
Increasingly, OEE will be part of a larger ecosystem of data and connected technologies. End-to-end shop floor connectivity will generate and share a comprehensive dataset that allows every process to work together harmoniously.
Combining this invaluable insight through an advanced strategic BI tool will correlate this data automatically to power new operational efficiencies. Artificial Intelligence can then suggest potential actions, provide guided interventions and uncover more insightful forecasts for better outcomes.
A Factory of the Future ecosystem works in harmony, rather than in the data silos. More insight is provided by combining tactical information, both real-time and historically, that is gathered through a shop floor gateway to allow streamlined analytics and strategic insight from a BI tool.
Artificial Intelligence and Machine Learning can be applied to understand the effects of various parameters, fault data, condition-based monitoring, and environmental or quality data. A connected factory ecosystem tackles a full digital optimisation process to find correlations without data mining and extraneous analysis.
The goal is to help customers optimise TPM, predict failures more frequently, predict forecasts more closely and accurately, and even predict behavioural elements like the profile of shift teams that perform best.
A comprehensive end-to-end multi-machine production line monitoring system combines all of the amazing and useful metrics of OEE, but uses smart technologies to add so much more to your future factoryโs ecosystem.
Optimisation for Every Area on the Shop Floor
Data correlation across the shop floor links machines and operators in an end-to-end smart connected factory. Every action and every process is digitally recorded, analysed and shared with the cloud.
Sharing real-time production data, as well as storing historical data, allows a connected factory to use company-wide information holistically to make intelligent and data-driven production decisions.
CamView State-of-the-art shop-floor IoT-enabled visualization takes slow-motion video captures of machine faults. Itโs grown from a need to record machine faults in real time so that operators can replay without standing at the line trying to catch the event or instance. More about CamView โ |
True Causal Loss Lineviewโs intelligent True Casual Loss algorithm automatically correlates a machine-level fault to its impact on that machine and your OEE score, adding insight to your plant data and enabling your team with actionable information to make data-driven decisions. More about True Causal Loss โ |
CIP Monitoring Use intelligent clean-in-place monitoring to eliminate common causes of CIP failure, identify savings from steps repeating and step overruns, reduce the use of effluent and cleaning materials, and improve the consistency and compliance of CIP processes. More about CIP Monitoring โ |
Line Balance Optimisation Control Automatic optimisation of machine restarts and recovery speeds can provide performance gains between 2-5%. LBO Control maintains the Critical Machine or bottleneck in a running state at its rated speed. When upstream or downstream equipment fails, automation maintains a running state as long as possible. More about Line Balance Control โ |
Built-in Management Routines Integrated meetings, compliance tracking and visibility of action effectiveness are used to efficiently identify performance gaps, find cause of greatest loss, pinpoint required actions, or set targets and measure effectiveness. More about Management Routines โ |
Use AI and Automation to Improve Operational Efficiency
Implementing AI on the shop floor isnโt all or nothing. All types of factories, no matter their level of connectivity, can benefit from Artificial Intelligence and Machine Learning.
Practical applications are a great starting point for Machine Learning technologies that save time on routine actions or correlate seemingly disparate pieces of data. When AI can transform insight into actions, it can shift the responsibility and authority of routine tasks from technicians to machine operators.
Machine Learning, as an element of AI, can provide automated insights that either take humans a long time to do โ or that humans cannot spot. This can be applied to machine or line performance to make more accurate predictions on planning outcomes.
The goal of the integration of AI is to provide useful insights faster, that leads to taking actions earlier to prevent downtime and losses. These insights can be applied to both chronic and sporadic issues.